A look behind the scenes into the pavement challenges and what options were considered for this paving application method for Champaign County, Ohio Engineer’s paving project. Read below to see why this cold mix paving product was the clear answer for this project.
THE PROJECT OVERVIEW
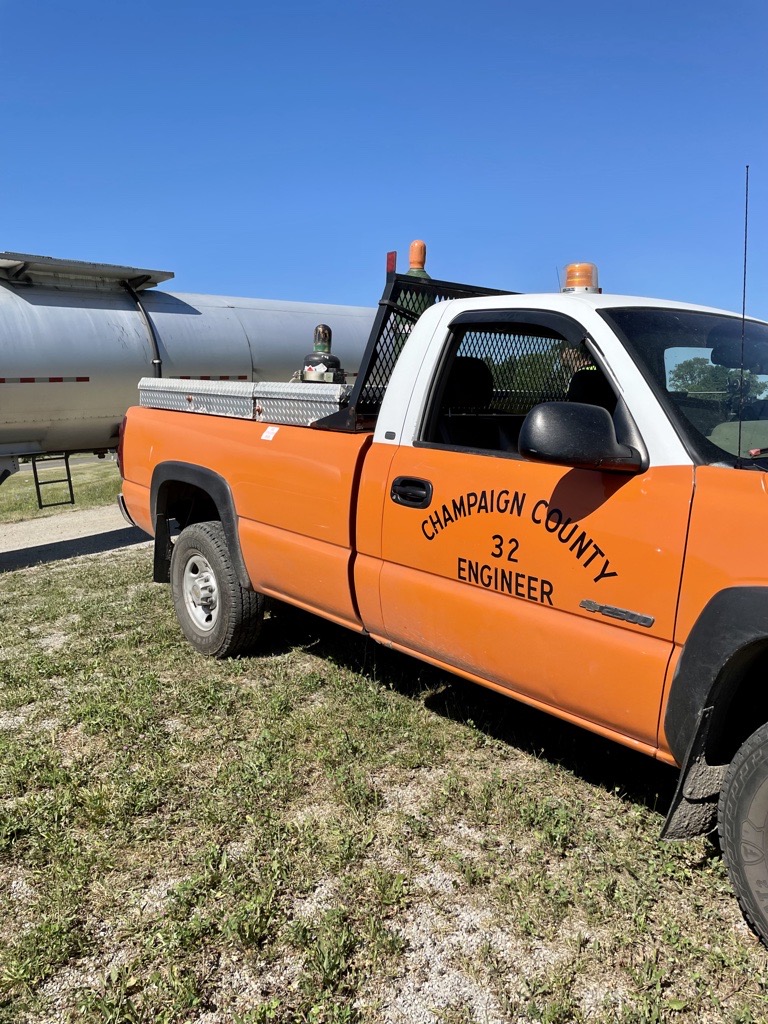
Located just northwest of Columbus, the maple tree-lined streets in Champaign County, Ohio remains an important industrial and manufacturing center. Not only do several headquarters in the horticulture & agriculture industries call this County home, but it also has a large Amish population. As you can imagine, the quality and condition of the County’s busy roads play a huge role in the day-to-day functioning of its organizations and residents. These rural “farm to market” roads must be resilient to keep the County running smoothly and safely. This summer, AMI was able to collaborate and support the County Engineer’s paving project decisions that led to nearly 30% savings.
Key members of the AMI team were able to present more economical and sustainable approaches as an alternative to a traditional full reconstruction. As AMI frontrunners for this county project, Rick Reynolds and Bruce Wehr were able to explain the different ways pavement methods can be more environmentally friendly and cost-effective solutions to other methods. During these conversations, success stories were shared which compared the different methods. Considering the needs of the County for this project, the AMI team also showed projected cost savings and the structural and environmental benefits of choosing an optimized method3. The overall recommendation was to perform a paving method called Cold Constructed Asphalt Pavement or CCAP®.
AN ECONOMIC ALTERNATIVE TO FULL RECONSTRUCTION:
COLD CONSTRUCTED ASPHALT PAVEMENT
Recognized as an incredibly versatile, budget-friendly, and environmentally sound choice for rural roads, Cold Constructed Asphalt Pavement (CCAP®) is a cold mix asphalt. CCAP® is created by combining aggregate and a chemically modified asphalt, mixed together at ambient temperature. This blend of gelled asphalt and additives, called CM-150, is mixed with pre-approved aggregate through a mobile mixing plant set up close to the construction site. The ability to blend different aggregates during the mixing process creates a mix that can be applied at various thicknesses.
“We are able to blend a variety of aggregates together to meet whatever need the agency has in resurfacing the road with this method. With this product, we can gel asphalt and add an antistrip to it, then we’re able to coat cold, wet stone.”
Bruce Wehr, AMI Sales Representative
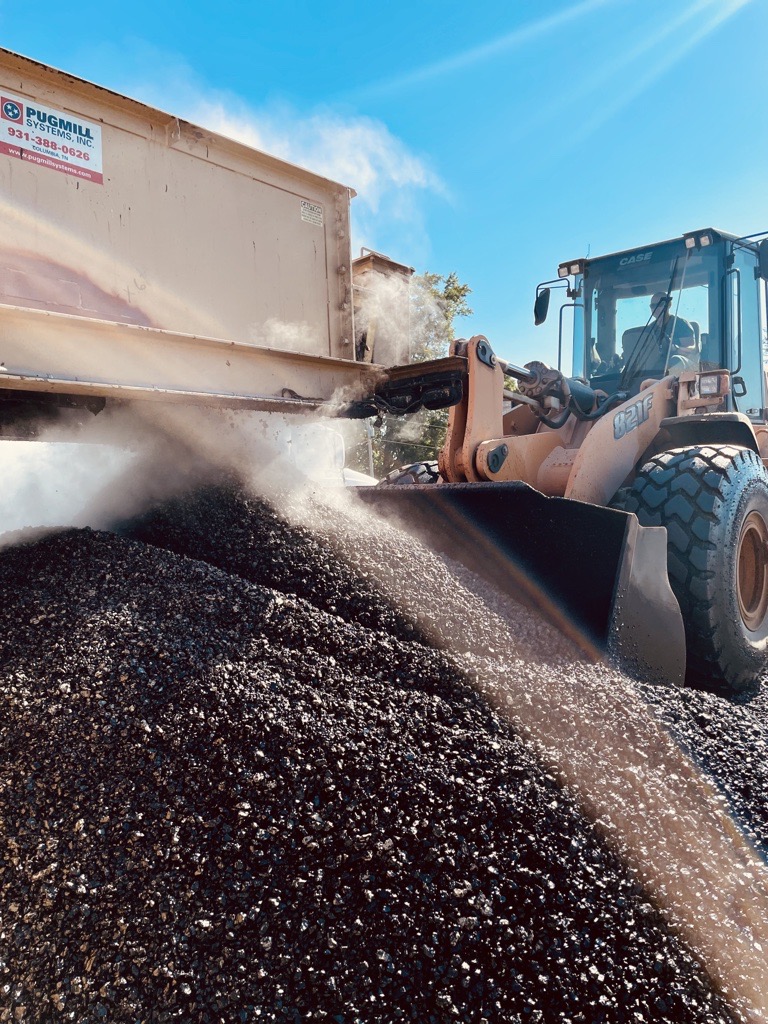
This gelled asphalt, or chemically modified asphalt, has different grades for different applications. This technology was developed at The Heritage Research Group labs in the late 1980’s. This method was created to replicate high float emulsions without water, keeping the film thickness higher, which is preferred1. Not only does this method eliminate water from the emulsion, but it also reduces run-off of the binder. The cold mix may be stockpiled for weeks or a few months. It can then be placed using a paver for road repairs such as patching potholes or adding a new layer to low-volume roads. A chip seal is often placed over the cold mix, which is planned to be laid next year for this project. CCAP® products have been proven to be successful in the laboratory and during field-based projects3. It has been thoroughly developed and proven with Job Mix Formulas (JMF), that produce years of performance on roads across the Midwest.
“It’s a very flexible product, resists cracking, and is durable under all types of traffic, everything from horse and buggies to trucks.”
Bucky Brooks, AMI
Agencies using this material are finding that pavement costs are reduced by as much as 30%. By implementing processes and materials like those experienced here with this CCAP® project, asphalt pavements deliver the performance that agencies, designers, owners, and drivers demand: an optimized solution for the entire community in Champaign County, Ohio.
BENEFITS OF THE CCAP® PROCESS
The CCAP® process not only has the potential to significantly decrease costs in pavement projects but will also improve efficiency and sustainability. CCAP® has an increased speed of construction and is more environmentally friendly than deep rehabilitation or reconstruction procedures. With the implementation of this durable & economical method, it is possible to keep costs manageable without affecting the overall quality of the road.
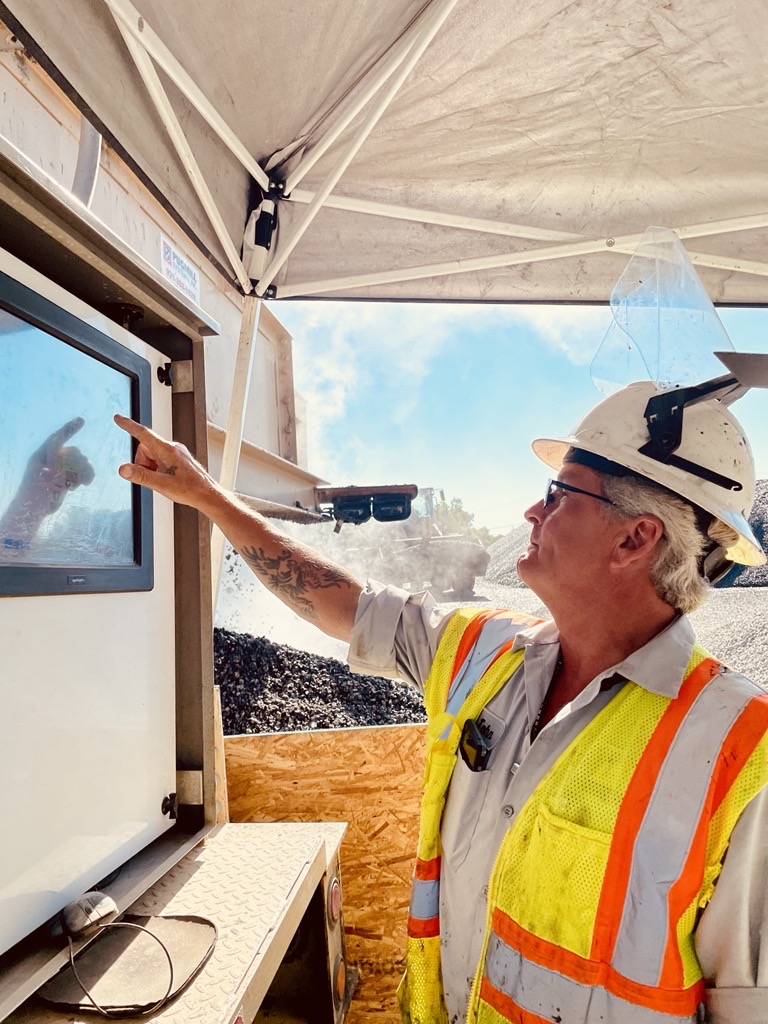
A summary of the recognized benefits of the CCAP® process includes:
- Remains flexible through cold weather, guarding against cracks and potholes
- Maintains durability in the heat of the summer, resisting flushing and tracking
- Grade is stiff enough to carry traffic, yet soft enough to workably flow through a paver
- Can be stockpiled for extended periods of time
- Ability of Agencies to Self-Perform, eliminating time constraints
- Antistrips & oils blended into mix to meet climatic & construction needs
- No tack coat is required due to film thickness
- No real compaction, effort only seating of aggregate
This Chemically Modified technology gives conventional asphalt better hot weather stiffness. The strong, angular aggregates carry load and do not affect the asphalt’s low temperature stiffness – it maintains flexibility at low temperatures. The gelled asphalt allows for increased film thickness, which in turn helps to extend the ageing process of the pavement. Most types of aggregate, whether wet or dry, can be coated due to the addition of the specially formulated anti-strip. This means that CM-150 is a component that is versatile enough to be used anywhere with virtually any aggregate. It also allows the use of any size open graded aggregate from ¼” to 2” or more to build roads from the base up or overlay existing pavements.2
“I have been involved with the application of CCAP® for thirty years and have grown to trust its capabilities as an asphalt overlay in many different traffic situations and not just as an application to use on rural roads. CCAP® offers a thicker film coating of gelled asphalt that allows increased volumes of both passenger vehicles and trucks”.3
Bucky Brooks, AMI Sales Manager
THE PROCEDURE: RECYCLING & RECLAMATION
The process for producing CCAP® mix starts with the asphalt binder and a chosen aggregate gradation. The binder is delivered to the project site where the cold mix is to be produced. Production of the mixture is then performed with a pug mill system at ambient temperatures resulting in low emissions and reduced energy consumption. The pug mill system allows a set amount of asphalt binder to combine with the aggregate. The finished CCAP® mixture is then loaded and delivered to the paving site or stockpiled until ready for placement.
“You can let this material sit on the ground for a few months. It has a long shelf life if stored properly.”
Cameron Porter, AMI Sales Representative
How is it produced? The Asphalt Materials, Inc. (AMI) product being used on this project was CM-150, supplied from our Oregon, Ohio plant. A pugmill is used to mix the aggregate and CM-150 cold, with no added heat necessary. The pugmill allows for a proper blending of the aggregates and appropriate proportioning of the CM-150 asphalt with the aggregate. The county is paving with this material full width, using locally sourced crushed aggregate. CCAP® may have tenderness on the first day of the project, depending on the climate specific conditions1. The third to the fifth day of the project is when CCAP® has its peak strength.
The construction procedure for the CCAP® mixes consisted of the following steps:
- A simple blend of crushed aggregate and CM-150 asphalt binder
- CM-150 begins with Multigrade (gelled) Asphalt that is specially formulated to meet specific climatic conditions
- A specific blend of oils is added to create CM-150 products to meet specific construction needs
- An anti-strip specially formulated for CM products is added at variable levels to assist in coating specific aggregates either wet or dry
- CM-150 mixes can be mixed and laid immediately or stockpiled for extended periods of time with no asphalt drain down or run-off concerns
- Mixes can be laid with a grader or conventional paver to achieve remarkable ride quality
- CM-150 open graded CCAP® mixes can stand up to all types of traffic including truck and higher volume traffic
- Under the right conditions and properly treated, these roads will last for years and years
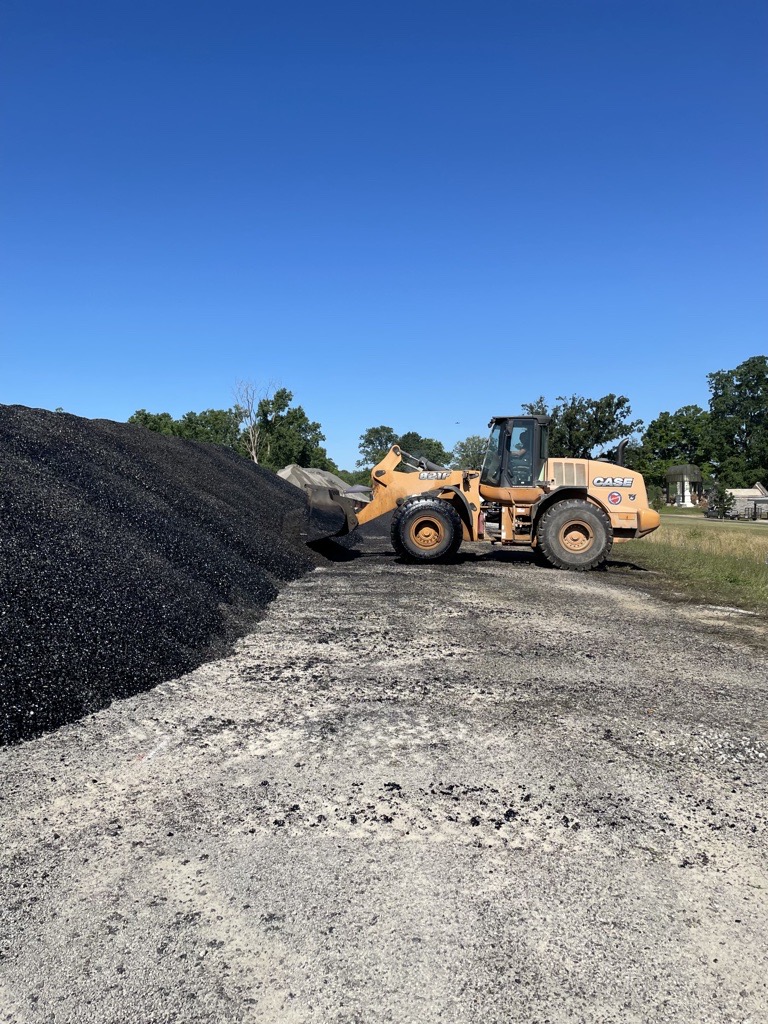
Equipment Required:
- Pugmill
- 2 Front End Loaders
- Dump trucks Conventional Paver
- 10 Ton Steel Drum Static Roller
- Chip Spreader/ Truck Mount Spreader to apply blotter aggregate
The Timeline:
- Starts at the Stockpile
- Paving train Placed with conventional paver
- Compaction
- Applying blotter aggregate
- Finished CCAP® product: ready for traffic, after compaction
THE BIG WINS
CCAP® construction is relatively easy for local crews to lay and maintain using standard asphalt paving equipment. CCAP® mix remains flexible through cold weather, guarding against cracks and potholes. In addition, this method still maintains durability in the heat of the summer, resisting flushing and tracking. Not only is this method rut and crack resistant, but it is also safe. By utilizing this material, the county was able to widen the road, or upgrading pavement width, which provides better safety overall.
“It’s great to be able make some safety improvements and this material does a great job of increasing the safety of the road.”
Steven McCall, P.E. Champaign County Engineer
This method of paving is such a unique process because it is stiff enough to carry normal traffic, while maintaining its softness to workably flow through a paver. Not only does CCAP® stay workable in cold temperatures, antistrips and oils are blended into the mix to meet climatic and construction needs. With CM-150 CCAP® mixes, even the worst pavements can be overlaid with little or no preparation, compared to a traditional Hot Mix Asphalt process that needs to be compacted first in order to gain its strength.
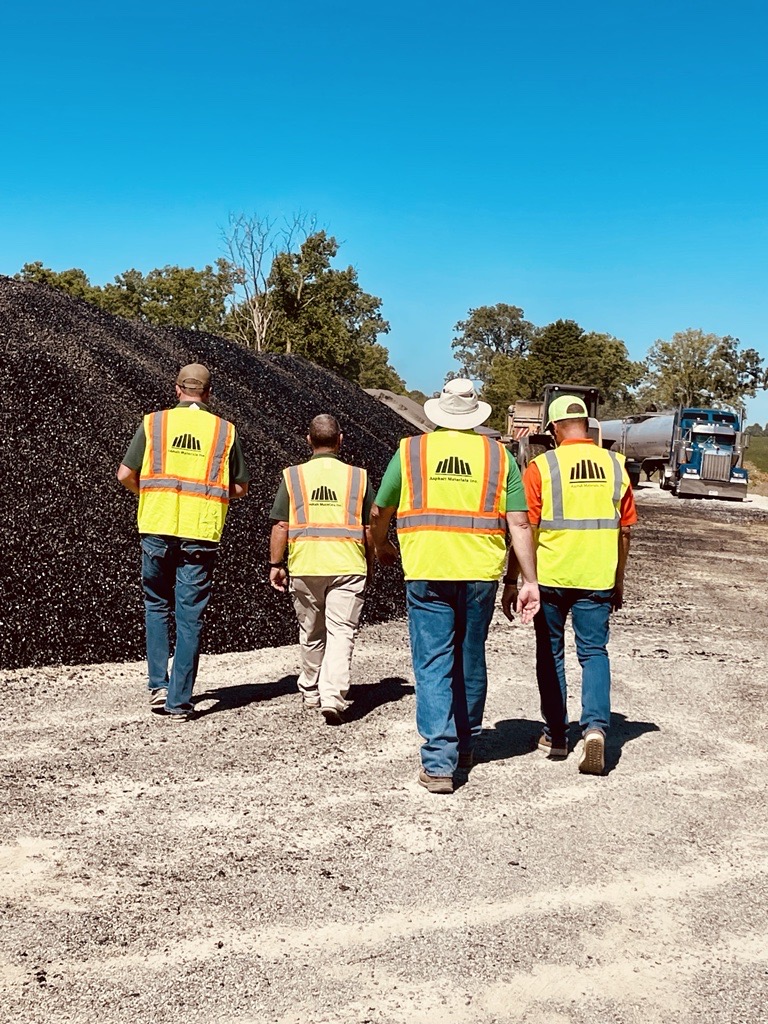
The benefits of having this material stockpiled are also notable. The key features of stockpiling CCAP® are that it is waterless – it has thicker films with no draindown during precipitation. There have been examples of stockpiles of the material extended for periods of time and used up to a year later.
Cost Comparison:
- 1 mile of Road at 18 feet wide placing 2 inches of mix
- Hot Mix Asphalt (110 lbs./sq. yd./inch)
- 1,162 Ton x $85.00/Ton = $98,770.00
- Cold Constructed Asphalt Pavement (85 lbs./sq. yd./inch)
- 898 Ton x $85.00/Ton = $76,330.00
Savings of $22,440.00 per mile
SUMMARY
CCAP® is part of Asphalt Materials’ AMIBIND™ Product Portfolio. A core strength of Asphalt Materials, Inc. (AMI) is the formulation, manufacturing, and research & development of asphalt binders and emulsions. Our Asphalt companies supply high-quality products and services which allows AMI to excel in pavement preservation techniques and construction services.
Asphalt Material’s AMIBIND™ CCAP® Products include:
• CM-150 Multigrade Asphalt
• CM-300 Multigrade Asphalt
Since 1980, our in-house R&D laboratory, the Heritage Research Group, has helped our industry, customers, and partners address and tackle our industry’s biggest challenges. Today, our labs provide innovative products, processes, and training to create longer-lasting, safer roads. We constantly seek new and inventive solutions by working closely with our customers and partners.
J-Band®, CCAP® and T-BOND® are registered trademarks of Asphalt Materials, Inc. AMIBIND™, AMIBOND™, AMICYCLE™, AMIGUARD™ and AMISEAL™ are trademarks of Asphalt Materials, Inc.
RESOURCES
1 https://thgrp.com/heritage-research-group/
2, Jason Wielinski, P.E. https://docs.lib.purdue.edu/cgi/viewcontent.cgi?article=4051&context=roadschool
Recent Comments