Many highway agencies recognize the benefits of using modified asphalts to reduce pavement distress and increase service life. A recent study from the Minnesota Department of Transportation (MnDOT) found that asphalt pavements with polymer-modified binders (PMBs) perform better than pavements with unmodified asphalt binders. They also found that modified binders are more cost-effective, even for local low-volume roads. While pavements with PMBs may cost more initially, performance is improved in the long run.
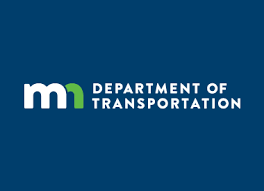
Research Methods
The research investigated the use of PG 58H-34 PMB binders (grade C) and PG58S 28 unmodified binders (grade B) for low-volume roads in Minnesota. Methods included analyzing historical pavement performance data to compare the field performance of modified and unmodified mixtures, in addition to laboratory experiments to compare the low-temperature cracking properties of polymer-modified and unmodified binders and mixtures commonly used in Minnesota. Based on the experimental results, a life-cycle cost analysis (LCCA) was performed comparing the use of polymer-modified and unmodified binders for low-volume roads in Minnesota.
The results showed that using PMBs for new construction is expected to extend the pavement service life by 6 years, and that using PMB is more cost-effective than using unmodified binders for low-traffic roads.
Sustainability Findings
Based on initial construction costs of each mixture, MnDOT researchers found that using PMBs could result in an estimated 14.4% cost savings over the pavement’s life.
Although the initial costs of using PMBs on low-traffic roads are greater than unmodified binders, the benefits outweigh the cost. Pavements that can achieve longer intervals without maintenance justify their higher costs. Parallel benefits of these high-performance asphalts include improved rutting resistance, less cold temperature cracking, improved mixture durability, and improved stripping resistance.
Find the MnDOT’s full study and its findings here.
AMI Prioritizes Sustainable Solutions
We have extensive experience in the production of polymer modified asphalts used for a variety of applications. Our process of manufacturing utilizes the most advanced technologies available to create polymer modified asphalts that meet customer and DOT requirements, ensuring complete satisfaction. We offer a variety of highly modified polymer modified asphalts.
“We see polymer-modified asphalt provide tremendous benefits, whether in hot mix asphalt (HMA) or in our preservation products,” said AMI Specialty Products Technical Director Todd Thomas.
“The performance-enhancing benefits are worth the cost.”
Some polymer modified asphalts in our AMIBIND™ product portfolio include:
- PG 52-34
- PG 58-28S
- PG 58-28
- PG 58-28H
- PG 58-28E
- PG 58-34S
- PG 58-34H
- PG 58-34V
- PG 58-34E
- PG 64-22
- PG 64-28
- PG 64-34
- PG 70-22
- PG 70-28
- PG 76-22
- PG 76-28
- PG 76-34
- PG 82-22
Additionally, we offer StellarFlex FR®, a highly polymer-modified specialty asphalt binder formulated for exposure to jet fuel and the enormous weight of slow-moving aircraft. As the first FAA-specified fuel-resistant asphalt pavement, it allows asphalt to resist damage from jet fuel and hydraulic oil, plus rutting and cracking.
Other Sustainable Asphalt Technologies
The MnDOT study results should give local road engineers confidence that using high-performance materials like PMBs is cost-effective, even on low-volume roads.
Void reducing asphalt membrane (VRAM) is an example of a materials approach to longer lasting roads and solving joint issues. VRAM is a high-polymer-modified asphalt binder that is placed at the intended location of a longitudinal joint prior to paving. As hot mix asphalt is placed over it, the VRAM becomes fluid and migrates up into the interconnected voids in the joint region of the mix. After compaction, VRAM makes the pavement impermeable to moisture while sealing the longitudinal joint itself.
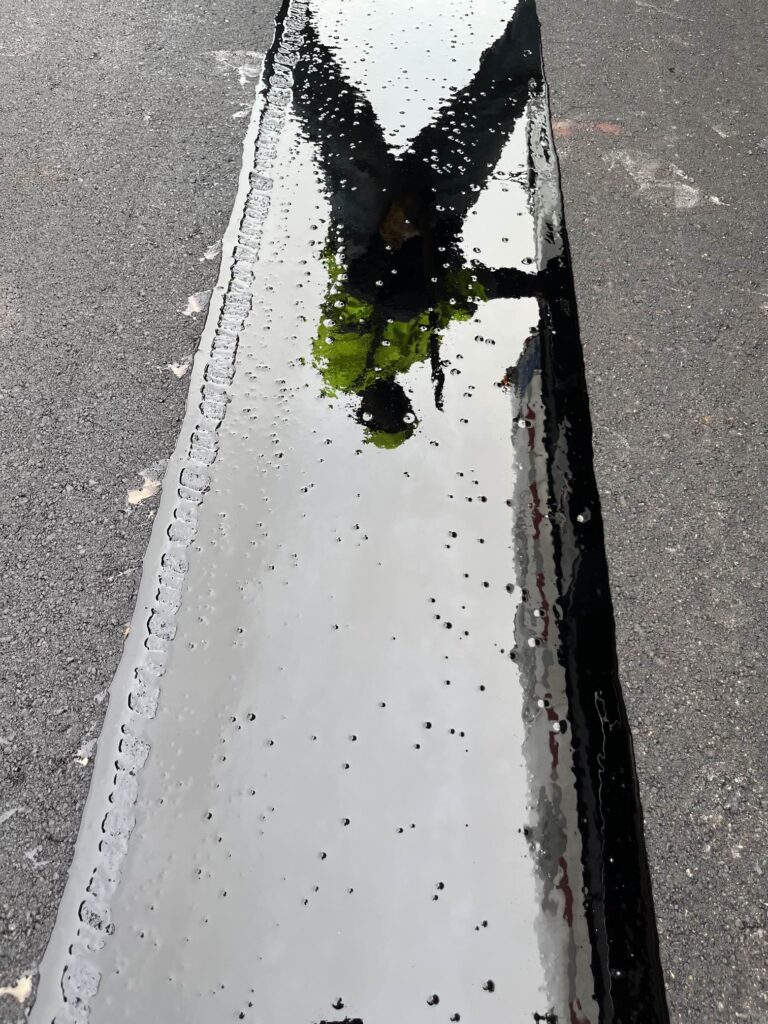
Asphalt Membrane Reduces Air Voids, Improves Performance
J-Band® is a void-reducing asphalt membrane (VRAM) product. VRAM migrates upward into the new HMA, filling air voids and reducing permeability. In an MnDOT-funded project, researchers evaluated the use of J-Band in an asphalt pavement on State Highway 22. Tests showed higher bond strength, lower permeability and air void levels, and improved crack resistance. 2
Historical data from previous VRAM projects shows that an investment in protecting the longitudinal joint helps roads last up to five years longer and delivers a return on investment of three to five times its cost. J-Band® is a VRAM product of Asphalt Materials, Inc. with a long performance track record dating back to 2002. J-Band was created in the labs of The Heritage Research Group in collaboration with state and local agencies and industry experts.
2 – http://www.mnltap.umn.edu/publications/exchange/2021/September/asphalt-membrane/index.html
Recent Comments