Looking ahead and seeking new opportunities to help create a sustainable future is a top priority at Asphalt Materials Inc. We understand the importance of sustainability now more than ever and will continue to review our projects and processes that are helping build sustainable infrastructure.
The Circular Economy is All Around Us!
The circular economy is a system that ultimately eliminates waste by using and re-using materials continuously. Asphalt starts as a byproduct, is used to create many of the roads we drive on, and when it is done correctly, it can last decades because of its durable nature. When the road needs to be reconstructed, the asphalt and aggregate that was originally used can be reused and reapplied.
The benefits and advantages of reusing asphalt and how it contributes to the circular economy are significant.
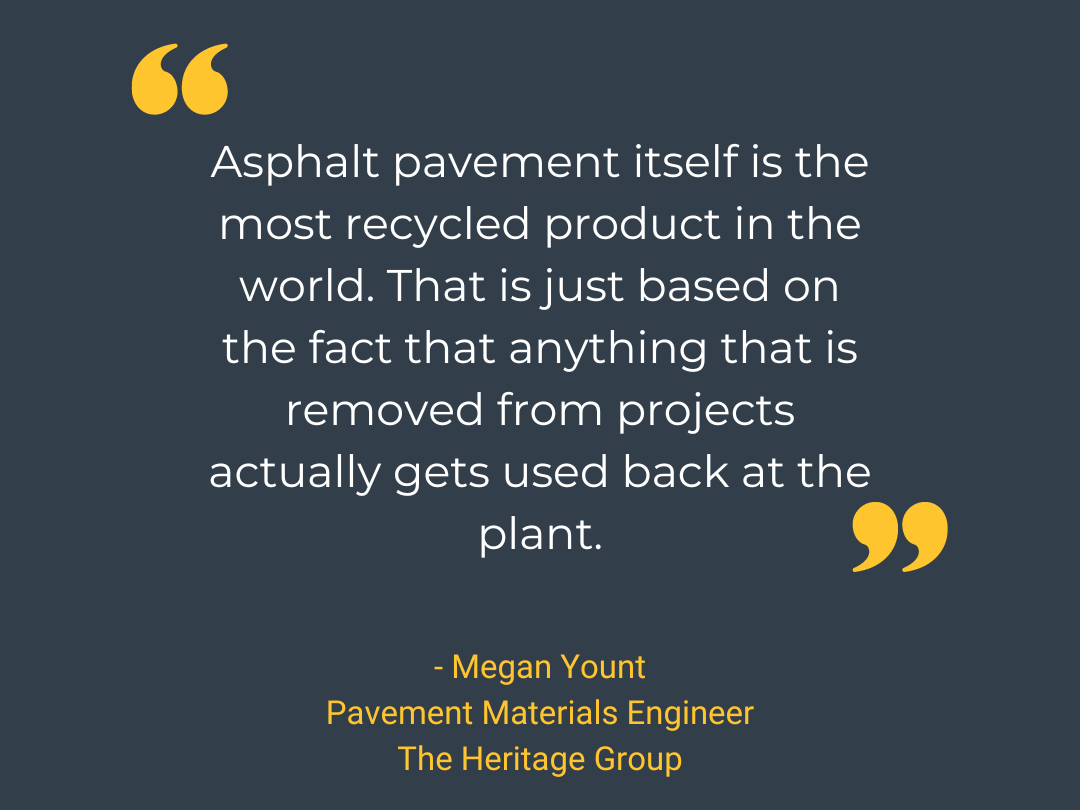
The recycling process of asphalt pavement saves both money and material. This is an example of a circular system, as asphalt pavement that is used and needs to eventually be removed, will be recycled and reused on future projects.
With a sustainable project method, such as CCAP®, it not only helps with recycling and reclamation but also leverages products and processes that are contributors to the circular economy.
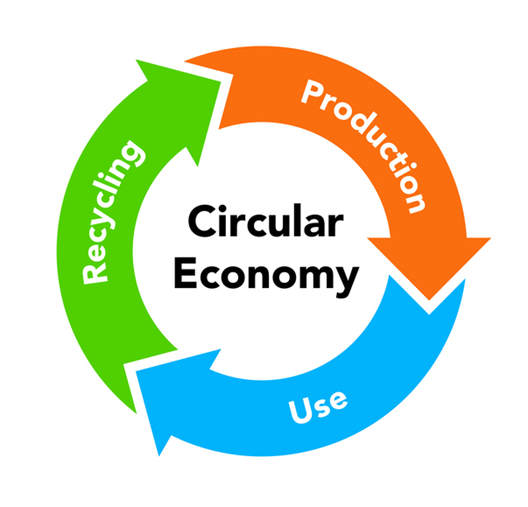
Sustainability Project That Saved Resources and Dollars.
CCAP® is durable enough to be placed on low and medium-volume rural roads, flexible enough to knead back together after being distorted by frost heaves, and economical. It can be used as a base course under hot mix asphalt, or as the riding surface when covered with a seal coat. Produced with local aggregates or RAP, which is accurately mixed with an asphalt emulsion in a portable pugmill, they are hauled & placed with conventional paving equipment. Across North America, CCAP® is a versatile, environmentally sound, budget-friendly choice for rural roads.
A Cold Constructed Asphalt Pavement (CCAP®) project that took place in Champaign County, Ohio is an excellent example of a project that will save infrastructure dollars and resources.
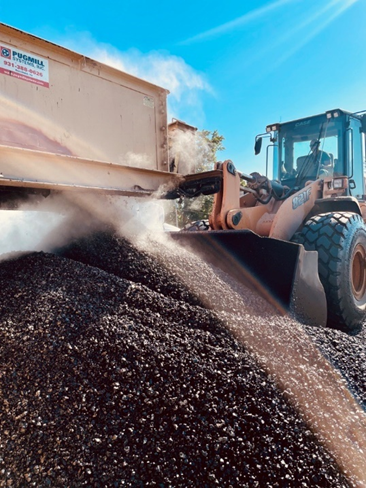
About this project:
This CCAP® project took place in Champaign County, Ohio just northwest of Columbus. With the county having such a high Amish population, the quality and condition of the roads are extremely important for the day-to-day activities of the driving public. As with other communities, their roads must be resilient to keep the county running smoothly and safely.
AMI team members for this project, Rick Reynolds and Bruce Wehr were able to present a more economical and sustainable approach to the county as an alternative to a traditional, full reconstruction method. They were able to explain how different pavement processes are more environmentally friendly and a more cost-effective solution versus alternatives. During planning sessions and conversations with county officials, success stories from previous AMI projects were shared, comparing the different methods.
Considering the needs of the county for this project, the AMI team also showed projected cost savings and structural and environmental benefits of choosing an optimized method. The overall recommendation was to perform a paving method called Cold Constructed Asphalt Pavement or CCAP®.
Why CCAP is a Future Trend.
The chemically modified technology used with CCAP® gives conventional asphalt better hot weather stiffness. The strong, angular aggregates carry the load and do not affect the asphalt’s low-temperature stiffness, while also maintaining flexibility at low temperatures. The gelled asphalt allows for increased film thickness, which in turn helps to extend the life of the pavement, by delaying the aging process of the pavement. Most types of aggregate, whether wet or dry, can be coated due to the addition of a specially formulated anti-strip. This means that AMI’s CM-150 is a component that is versatile enough to be used anywhere with virtually any aggregate. It also allows the use of any size of open-graded aggregate from ¼” to 2” or more to build roads from the base up or by overlay on existing pavements.
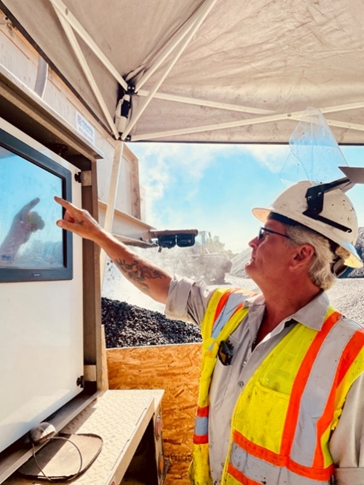
Some of the recognized benefits of CCAP include:
- Remains flexible through cold weather, guarding against cracks and potholes
- Maintains durability in the heat of the summer, resisting flushing and tracking
- Grade is stiff enough to carry traffic, yet soft enough to workably flow through a paver
- Can be stockpiled for extended periods of time
- Ability for Agencies to Self-Perform, eliminating time constraints
- Antistrips & oils blended into mix to meet climatic & construction needs
- No tack coat is required due to film thickness
- No real compaction effort, only seating of aggregate
The procedure of cycling and reclamation is what makes this process as successful as it is! The process for producing CCAP® mix starts with the asphalt binder and a chosen aggregate gradation. The binder is delivered to the project site where the cold mix is to be produced. Production of the mixture is then performed with a pug mill system at ambient temperatures resulting in low emissions and reduced energy consumption. The pug mill system allows a set amount of asphalt binder to combine with the aggregate. The finished CCAP® mixture is then loaded and delivered to the paving site or stockpiled until ready for placement.
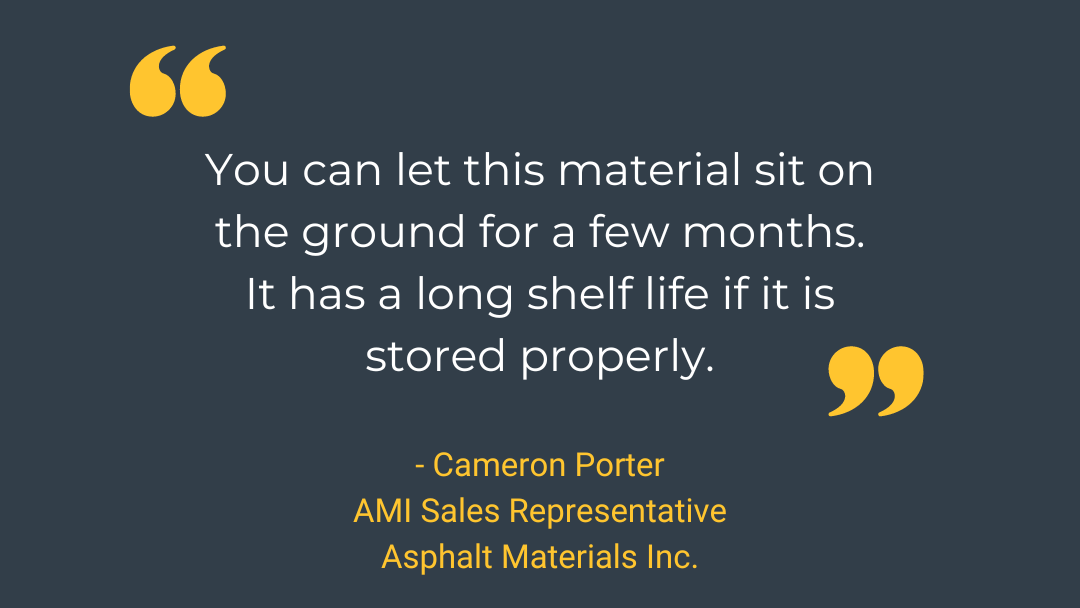
How is it produced? The Asphalt Materials, product being used on this project was CM-150, supplied from our Oregon, Ohio plant. A pugmill is used to mix the aggregate and CM-150 cold, with no added heat necessary. The pugmill allows for a proper blending of the aggregates and appropriate proportioning of the CM-150 asphalt with the aggregate. The county is paving with this material full width, using locally sourced crushed aggregate. CCAP® may have tenderness on the first day of the project, depending on the weather conditions. In the first 3-5 days of a project is when CCAP® will reach peak strength.
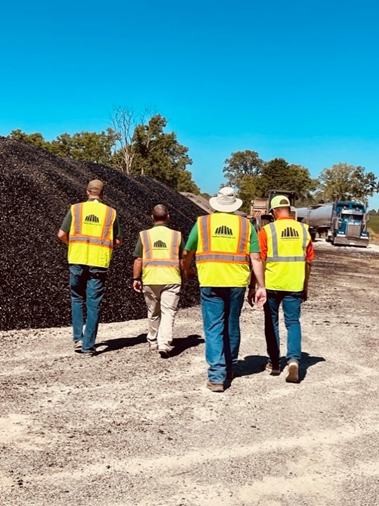
CCAP® is part of Asphalt Materials’ AMIBIND™ Product Portfolio. A core strength of Asphalt Materials, Inc. (AMI) is the formulation, manufacturing, and research & development of asphalt binders and emulsions. Our Asphalt companies supply high-quality products and services which allows AMI to excel in pavement preservation techniques and construction services.
Asphalt Material’s AMIBIND™ CCAP® Products include:
• CM-150 Multigrade Asphalt
• CM-300 Multigrade Asphalt
Since 1980, our aggregate, asphalt and construction teams have been supported by our in-house R&D laboratory, the Heritage Research Group (HRG). HRG helps our industry, customers, and partners address and tackle our industry’s biggest challenges. Today, our labs provide innovative products, processes, and training to create longer-lasting, safer roads. We constantly seek new and inventive solutions by working closely with our customers and partners.
If you are interested in finding a plant near you, fisit our locations tab and contact your nearest sales team member to learn more.
J-Band®, CCAP® and T-Bond® are registered trademarks of Asphalt Materials, Inc. AMIBIND™, AMIBOND™, AMICYCLE™, AMIGUARD™, AMISEAL™ are trademarks of Asphalt Materials, Inc.
Sources:
https://www.driveasphalt.org/why-asphalt/asphalt-delivers
https://www.driveasphalt.org/resources/perpetual-pavement
https://thgrp.com/heritage-research-group/
Jason Wielinski, P.E. https://docs.lib.purdue.edu/cgi/viewcontent.cgi?article=4051&context=roadschool
https://www.youtube.com/watch?v=GpkAz–QX10
Recent Comments