Let’s take a look behind the scenes into the pavement problems, what options were considered, and why recycling was the clear answer for Dundee High School pavement project in Monroe County, Michigan.
The Project Overview
Located in Southeast Michigan, the newly constructed Dundee High School campus opened in the Fall of 2001. Since that time, the parking lots had been neglected with only minor maintenance over the past 20 years. Fast-forward to 2018, where we see Dundee Public Schools in search of an answer to their parking lot pavement problems. The result? A well-thought-out decision that led to savings of nearly 500 hundred thousand dollars.
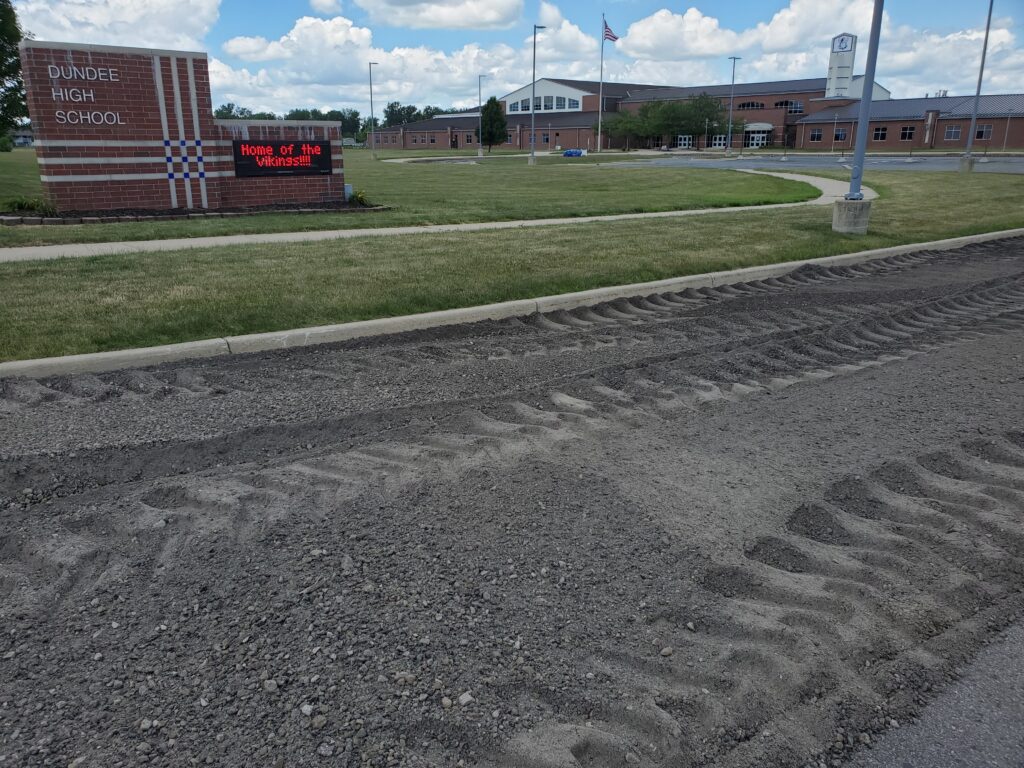
In 2019, a 1969 Dundee High School graduate donated $1 million to the Dundee Community School Board to be used toward a new athletic complex1. After 85 years of playing prep football in the same location, Dundee officially closed the doors on its stadium with plans to move into a brand-new athletic complex. The plans for the Craig Family Athletic Complex included essential pavement improvements on the campus for its parking lots.
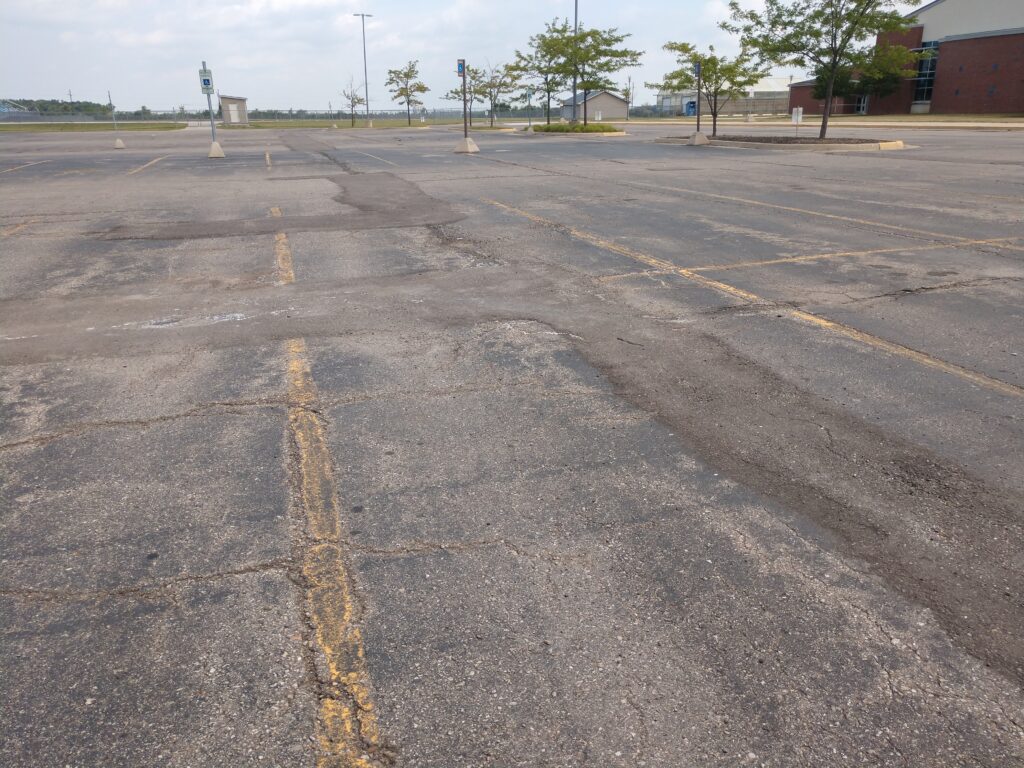
The initial scope of this pavement project was for complete removal and replacement of poor areas, essentially reconstructing portions of the entire parking lot. Realizing there must be a better, more cost-effective solution, in the spring of 2018, a Dundee School Board member and project consultant contacted Asphalt Materials, Inc. to discuss possible cost-saving options for reconstructing the campus parking lots.
Meetings were held where the AMI team presented alternative options. Scott Assenmacher, P.E. spearhead this project and utilized tools within roadresource.org to explain the different ways recycling methods were a more environmentally friendly and cost-effective solution. During these conversations, success stories were shared which compared the different methods. Using real data, Scott was able to utilize Sustainability and Structural Calculator tools to show projected cost savings, structural benefit, and environmental benefits of choosing an optimized recycling solution.
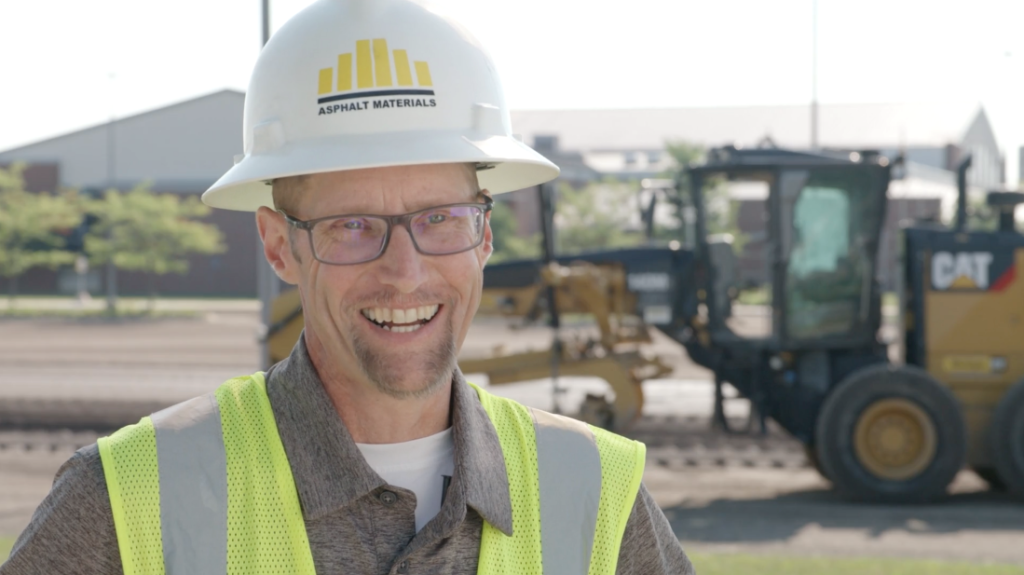
“They’ve been talking for 3-4 years on how to tackle this project without the big price tag of a more traditional fix. We got involved early on and landed on a recycling method that utilizes existing materials that have been in place & paid for, just tired and old and ready for a revamp.”
Scott Assenmacher, P.E. and AMI lead for project
In Fall of 2019, Heritage Research Group performed sampling of the parking lots for the high school. The existing parking lot consisted of an average of 4.7 inches of Hot Mix Asphalt (HMA), over 3-6 inches of crushed aggregate base. Common failures throughout the site included full depth cracking and stripping within the pavement. Drainage conditions were adequate for a cold recycling treatment. Dynamic Cone Penetrometer (DCP) testing was performed to estimate base and subgrade strength.
The overall recommendation was to perform a recycling method called Full Depth Reclamation (FDR), a 6-inch recycling treatment utilizing engineered emulsion. Isolated areas showed potential for full depth patching of the underlying subgrade and base, using structural fill. This recommendation led to the development of project bid documents in the Spring of 2020. However, shortly after, the project was delayed due to the unknown additional expenses and nature of the COVID-19 pandemic.
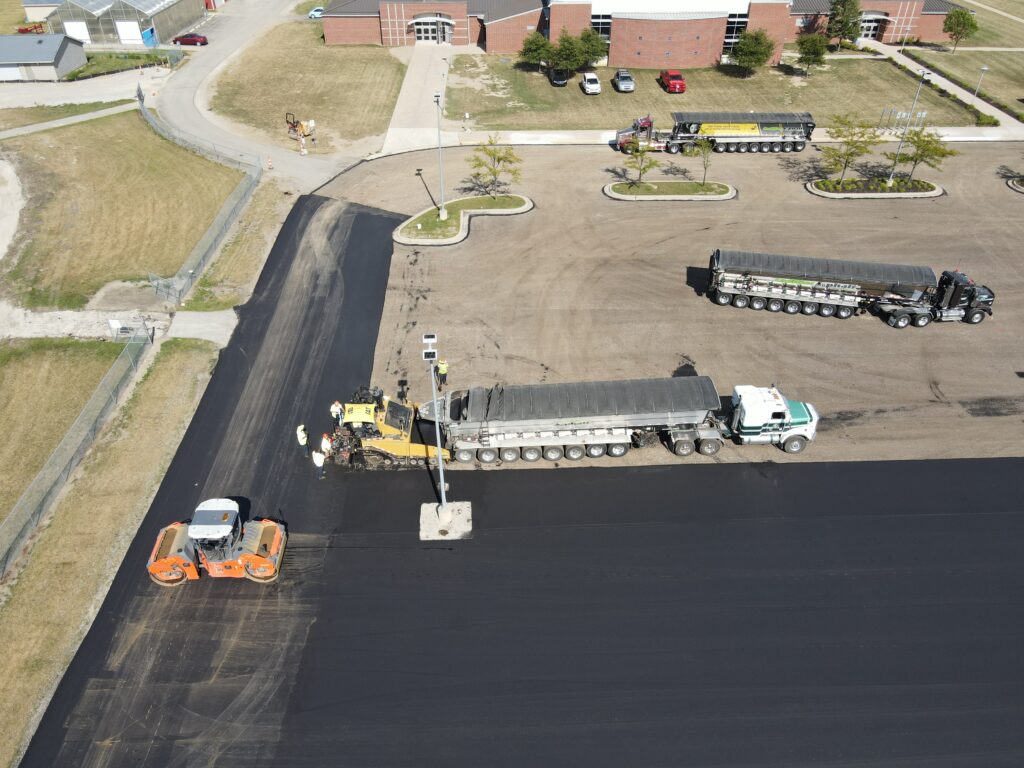
“When COVID hit, it just completely derailed all the work that we had done. We’re thrilled to be able to restart the project and thrilled to be able to continue this work that is so important for our community, for students, and for the future of Dundee.”2
Edward Manuszak, former Dundee Superintendent
Announced in the Summer of 2021, the project was resurfaced, and bids were developed with the intent of construction happening in 2022. While the COVID-19 pandemic was a major setback for this project, the excitement for the campus renovations was present in the community once again.
An Alternative to Deep Rehabilitation: Full Depth Reclamation
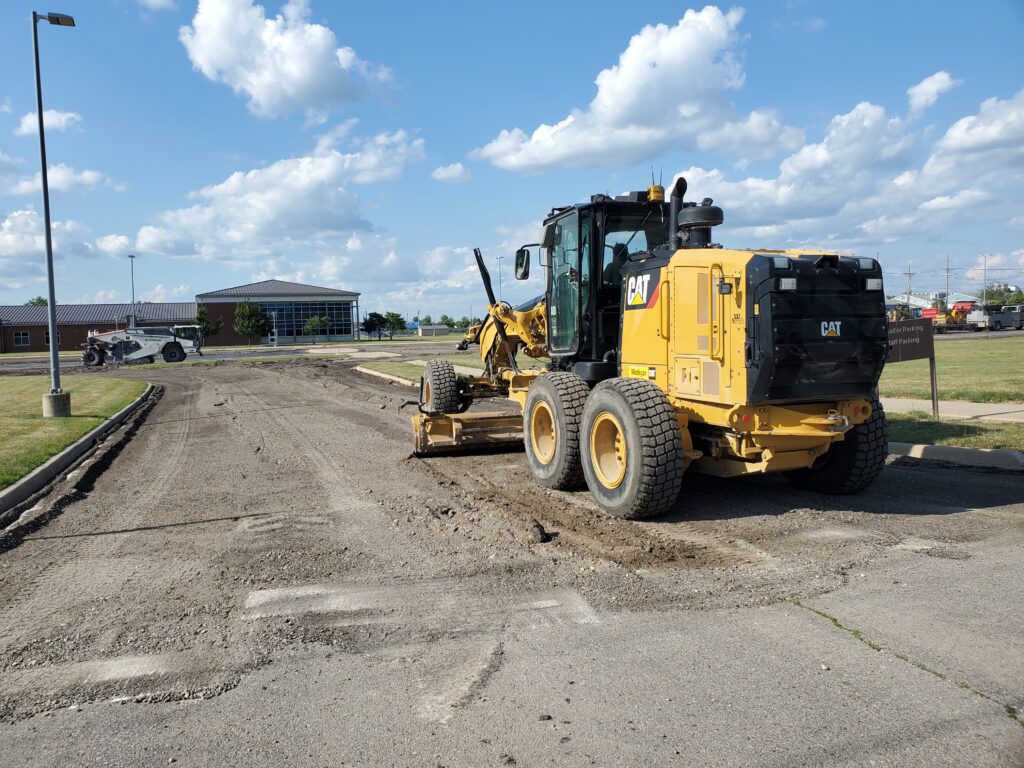
Recognized as a cost-effective, long-lasting greener alternative to deep rehabilitation or removal and replacement techniques, Full Depth Reclamation (FDR) is an engineered rehabilitation technique where the full thickness of the asphalt pavement and a predetermined portion of the underlying materials (base, subbase, and/or subgrade) is uniformly pulverized and blended to provide an upgraded, homogeneous material. The reclaimed materials may be improved and strengthened by using Mechanical, Chemical or Bituminous stabilization3. FDR isn’t only for roads in poor condition, it is also a viable design process for increasing the structural capacity of a pavement in good condition.
Benefits of the FDR Process
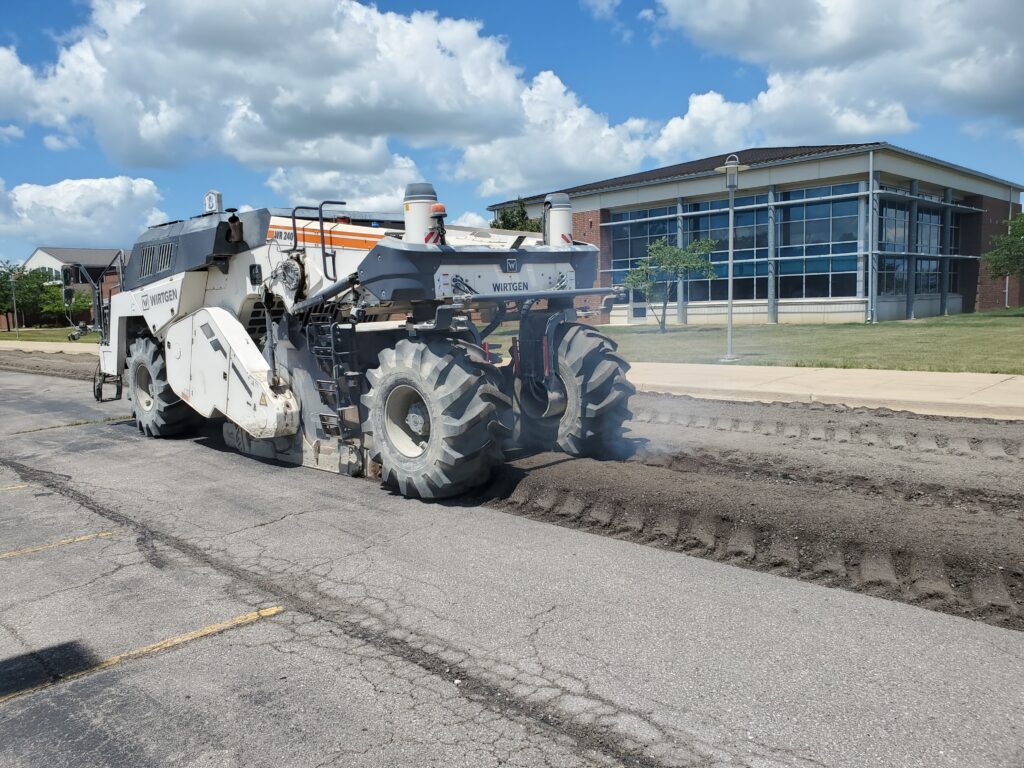
The FDR process has an increased speed of construction and is more environmentally friendly than deep rehabilitation or reconstruction procedures. For example, FDR cuts down on greenhouse gases by reducing and/or eliminating the use of new materials3. Most or all existing on-site materials can be used in the FDR process. By eliminating or reducing the use of new materials and by using on-site materials, there is no need to dispose of any materials. With the implementation of this sustainable method, it is possible to significantly decrease costs without affecting the quality of the road.
A summary of the recognized benefits of the FDR process includes:
- 40 to 80% less expensive than alternative reconstruction techniques
- Importing and exporting of materials can be reduced by 90%
- Reuses up to 100% of existing materials
- Same day return to light traffic
- Up to 25 years of life extension
The Procedure: Recycling & Reclamation
The construction procedure for the FDR treatment consisted of the following steps:
- Pulverization of the existing bituminous material and a portion of the underlying base material to achieve a total stabilization depth of 6.0 inches
- Grading and compacting the pulverized material across the final width of the pavement
- Injecting a 6.0-inch FDR treatment with engineered emulsion
- Grading and compacting the injected material across the final width of the pavement
- Once the final cure of the FDR is achieved, applying a surface treatment
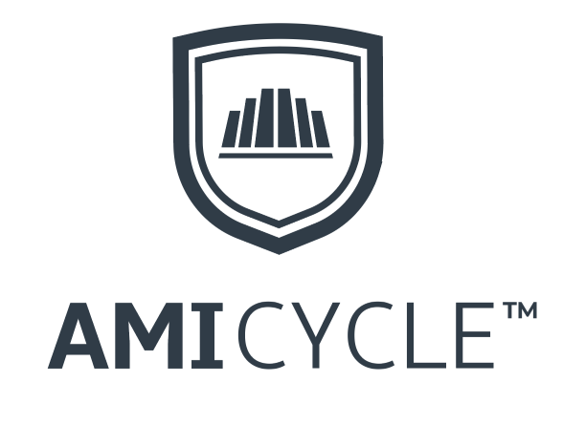
FDR is the process of pulverizing the full thickness of the asphalt pavement and a predetermined portion of the underlying materials (base, subbase and/or subgrade) with a reclaimer. If no stabilizing agents are required, a single pass is often sufficient to uniformly pulverize and blend the materials. If a stabilizing agent is used (chemical or bituminous), it is typically added and mixed during a second (mixing) pass of the reclaimer.
Prior to the mixing pass, the pre-pulverized material should be compacted and shaped. After mixing, the pulverized and mixed material is bladed and shaped, moisture conditioned for compaction, and compacted using a padfoot, smooth drum and/or pneumatic-tired compactors4. The reclaimed materials are then trimmed to final grade and allowed to cure until sufficient strength is obtained to carry the anticipated traffic.
The Timeline
The evolution of this recycling project spans more than 3 years:
- FDR project bid documents are developed in Spring of 2020
- COVID-19 hits in Spring of 2020, delaying the project due to the unknown additional expenses of the pandemic
- Summer of 2021, Christman Construction Company took over as lead consultant and with the help of AMI, developed bid documents for the DHS parking lots FDR with the intent for construction in 2022
- DHS still recognized the value and multiple benefits of the recycling option and directs Christman to move forward with the FDR solution
- Project is awarded to Cadillac Asphalt, LLC as the general contractor and Wadel Stabilization, Inc as the recycling subcontractor
- While school is out of session, the project commences in the summer of 2022
- Final surface course of HMA completed in time for start of classes in September of 2022
The Big Wins
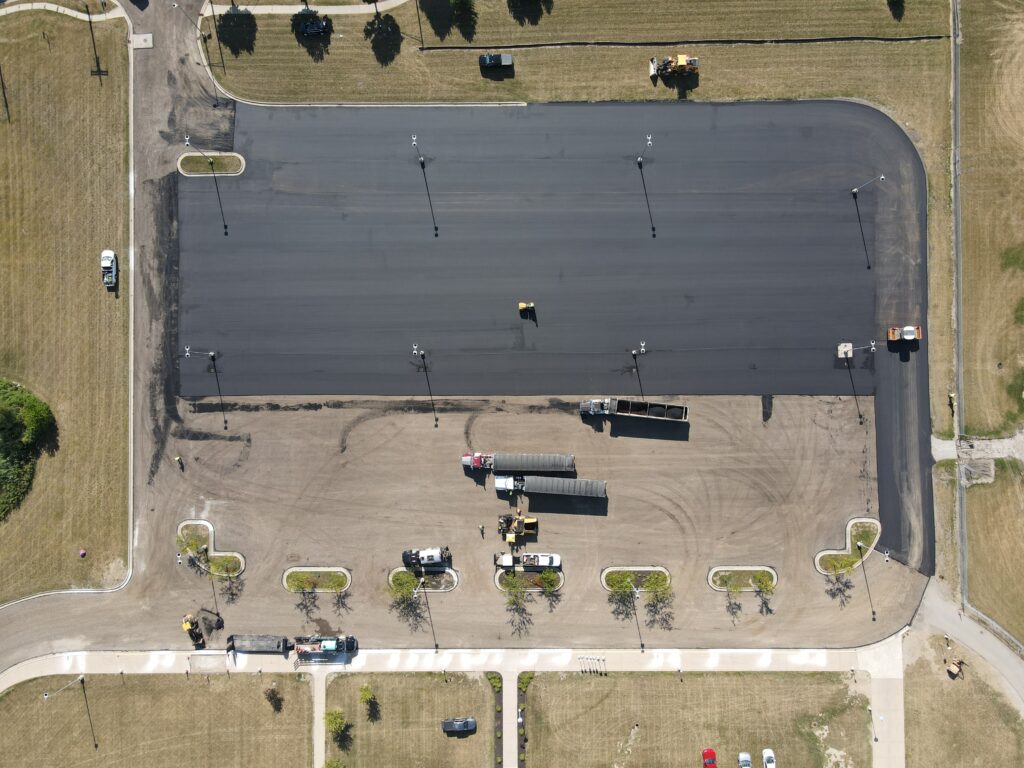
Dundee High School was able to recognize a cost savings of $490,000 while increasing the overall structural number by 0.52 by selecting a recycling approach in lieu of a traditional removal and replacement approach. Following this approach, allowed DHS to fund other much-needed improvements to the school grounds.
The recycling solution also allowed environmental savings through a reduction in greenhouse gas emissions of 13%. (*Using the Road Resource Sustainability Calculator)6
Because the parking lots are for a public high school, the window of construction during the summer is limited, to avoid any construction work while school is in session. Utilizing the FDR recycling approach also allowed a time savings of at least two weeks, providing a more comfortable window to avoid conflicts during times of heavy staff, student, and bus traffic.
After optimizing the recycling solution, the parking lots still had an excess volume of RAP that they were able to repurpose for other needs within the school grounds.
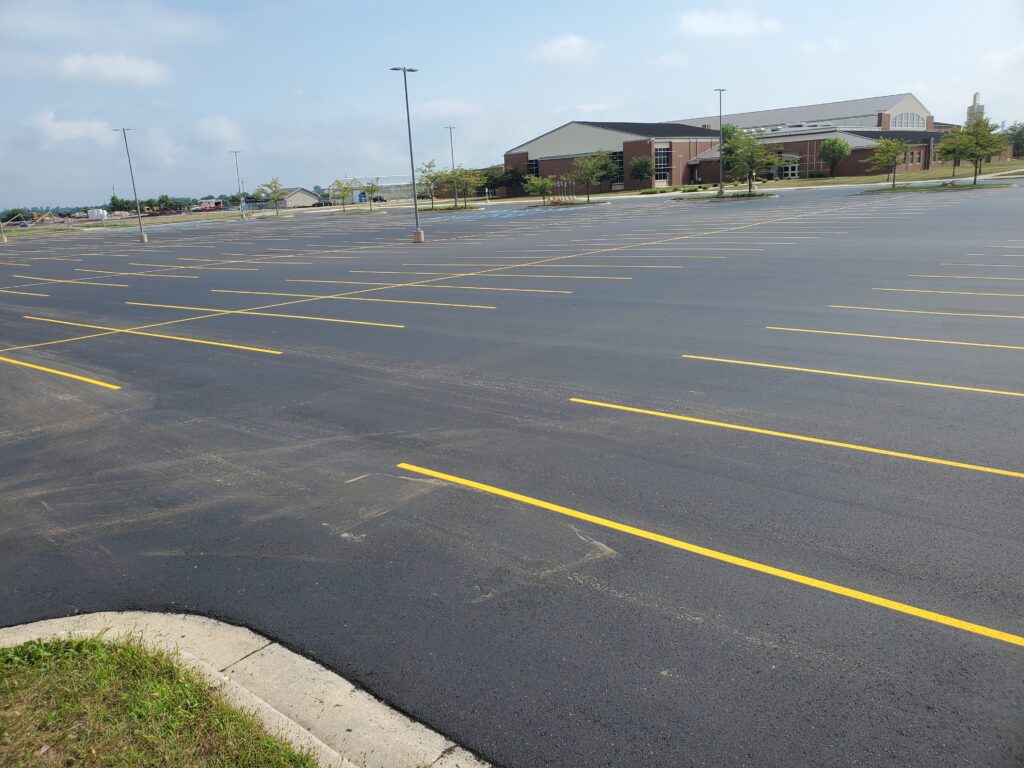
Dundee Public Schools also look forward to soon renewing their school millage bond and showing continued success in their current improvement plans with the Craig Family Athletic Complex. Additionally, other school grounds improvements, including the new and improved parking lots, on time and within budget, will encourage continued support for future funding.
Scott’s hard work for documenting this project was proudly submitted as a 2022 ARRA Special Recognition Award nomination for the outstanding contributions to the Asphalt Recycling and Reclaiming industry7. The award will be presented at the 2023 AEMA-ARRA-ISSA 47th Annual Conference to be held in Litchfield Park, AZ February 27 – March 3, 2023.
Summary
Recycling was the clear solution for the DHS parking lots improvements challenge. Using FDR as the recycling solution created some big wins, including cost-savings, environmental benefits, and time savings. The project’s success will gain public buy-in and support from Dundee Public Schools and the Dundee School Board for future bond funding projects.
The smart decision to use FDR method for this pavement project was due to all the contributors who had meaningful conversations over the 4-year duration of this community project.
Owner:
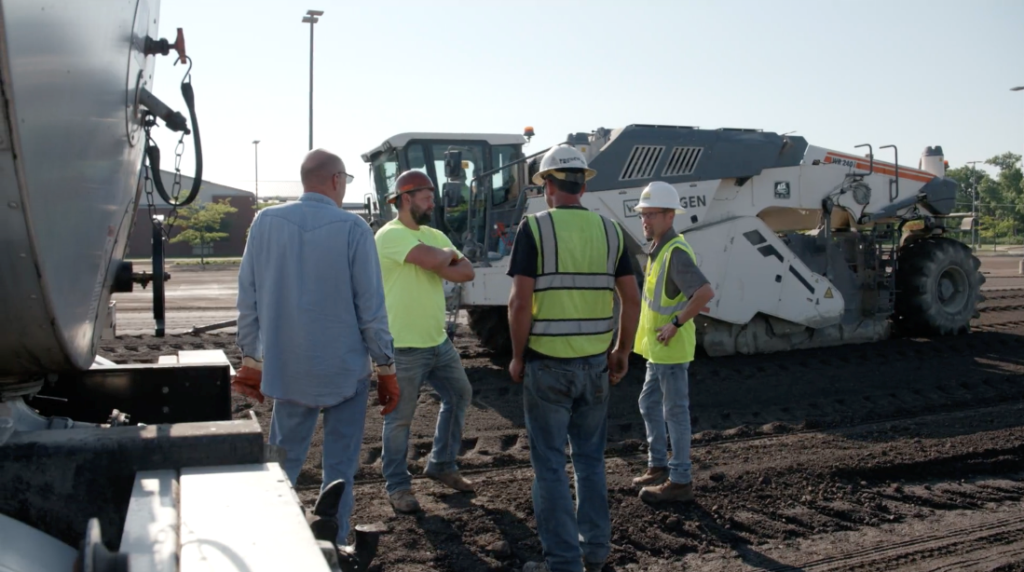
- Dundee Public Schools
Contractors:
- Wadel Stabilization, Inc.
- Cadillac Asphalt, LLC
Consultants:
- The Mannik Smith Group, Inc.
- Christman Company
Emulsion Supplier:
- Asphalt Materials, Inc.
Lab Support:
- Heritage Research Group
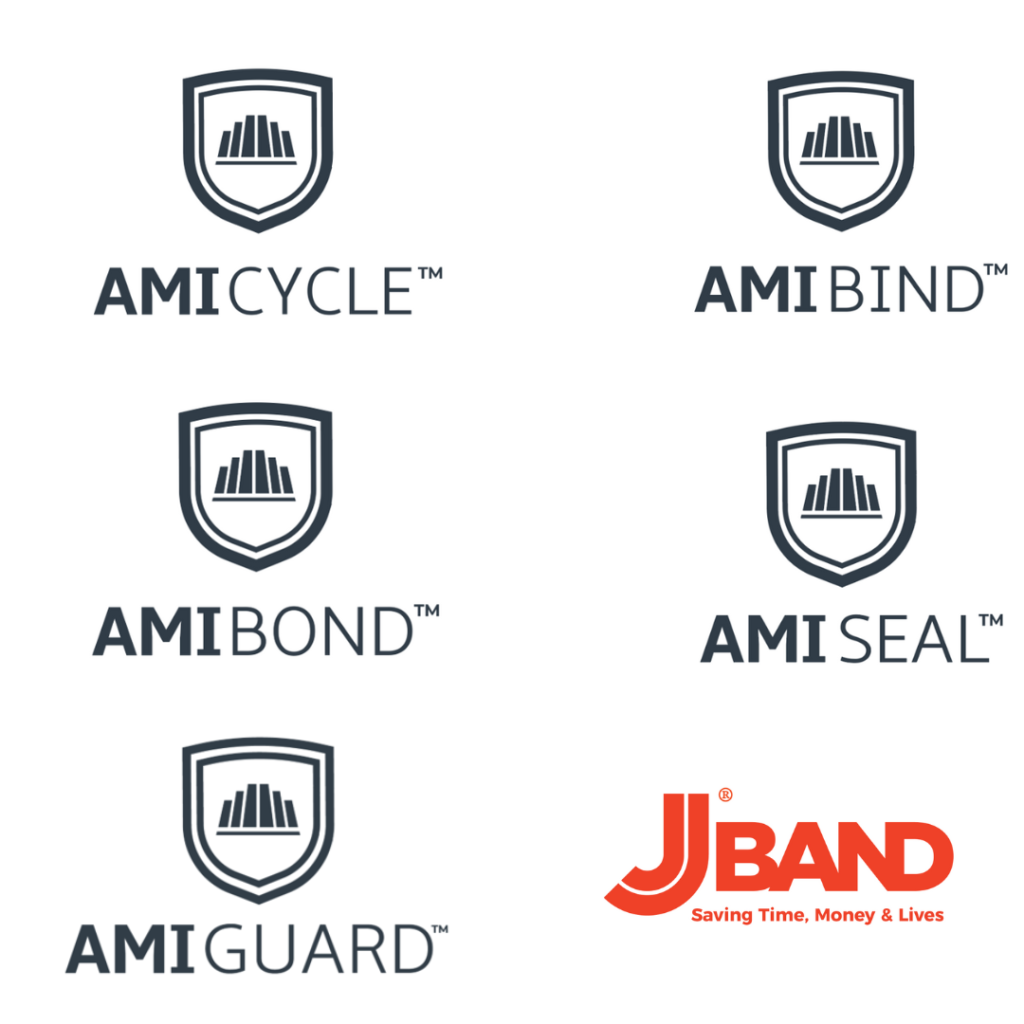
For more information about this project, see our overview video that explains the significant benefits Dundee community was able to achieve by thinking outside the box and asking for alternative solutions.
If you’d like to see these benefits in your next pavement project, reach out to our team to discuss options for your communities.4
J-Band®, CCAP® and T-Bond® are registered trademarks of Asphalt Materials, Inc. AMIBIND™, AMIBOND™, AMICYCLE™, AMIGUARD™, AMISEAL™ are trademarks of Asphalt Materials, Inc.
Resources
AMI Michigan Sales Team, Scott Assenmacher, P.E.
Superintendent for Dundee Public Schools, Scott Leach
1
2
3
https://roadresource.org/treatment_resources/full_depth_reclamation?page=about#tqm-main
4
https://asphalt-materials.com/products/
5
https://roadresource.org/treatment_resources/full_depth_reclamation?page=about_cost#tqm-main
6
https://roadresource.org/preservation/calculator
7
Recent Comments