On August 18th, a Chip Seal project took place in Gaston, Indiana. This project was completed by the Delaware County Highway Department. Chip seals are used to prevent water intrusion into a pavement and create a high friction surface for safety. Chip seal emulsions can be polymer modified to improve aggregate retention and provide for a quicker return to traffic.
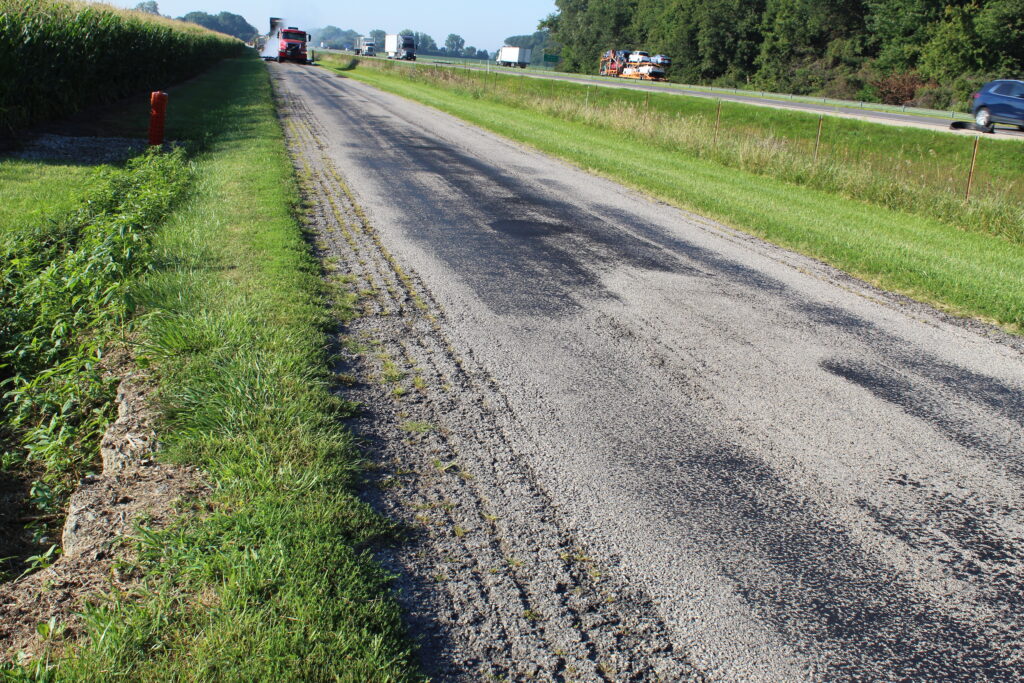
The process for this project began with a project selection, which was guided by an asset management plan. Next, the pavement preparation took place, which included addressing any drainage issues, patching as needed, be-berming if needed, sweeping of the pavement surface, and scheduling of materials including aggregate and the delivery of the asphalt-emulsion. After this, the application began.
The distributor applies a specified amount of the asphalt-emulsion. For this project, AMI’s AE-90S was used across the full width of the roadway.
AMISEAL™ Product Portfolio
AMI’s AMISEAL™ product portfolio includes chip seals, fog seals, cape seals, among others. You can view more on our products page here on this website.
Other AMI Chip Seals include the following:
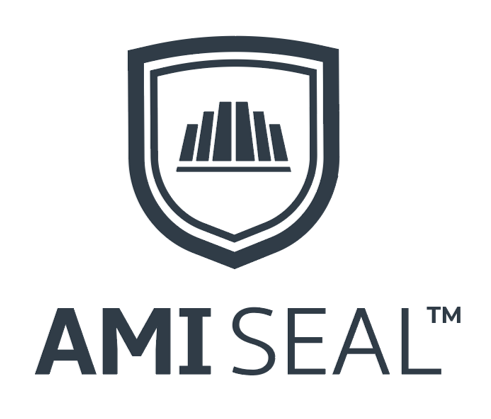
Products (neat emulsion):
• AE-150 • AE-200
• AE-300 • AE-90
• CRS-2 • HFE-150
Products (polymer modified emulsion):
• AE-90S • CRS-2P
• CRS-P • HF-P
Products (Chemically Modified Asphalt):
• CM-90
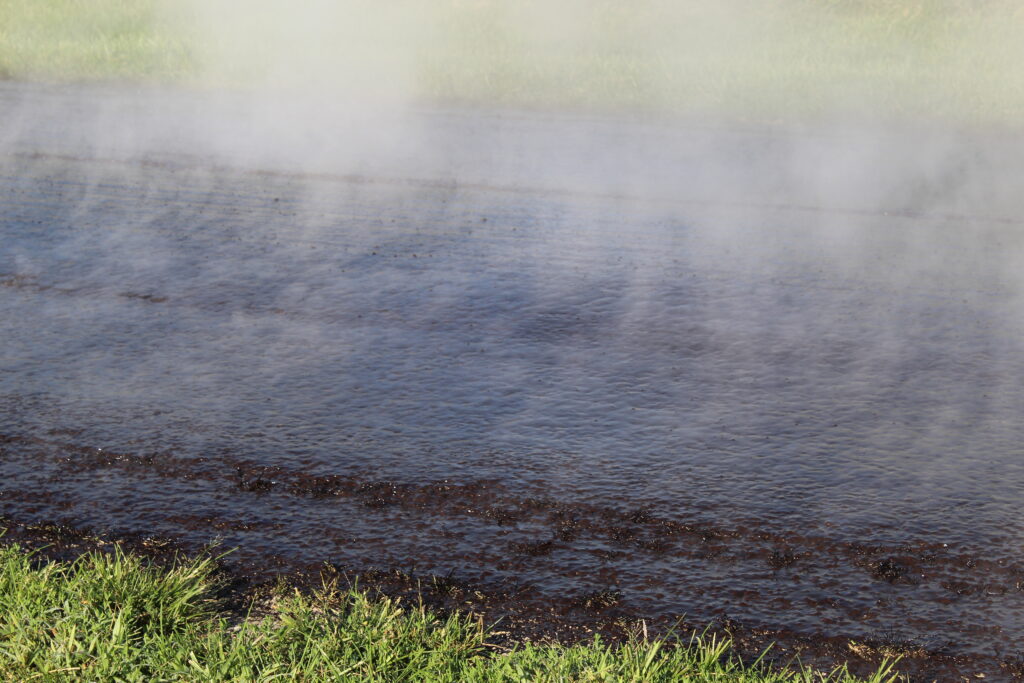
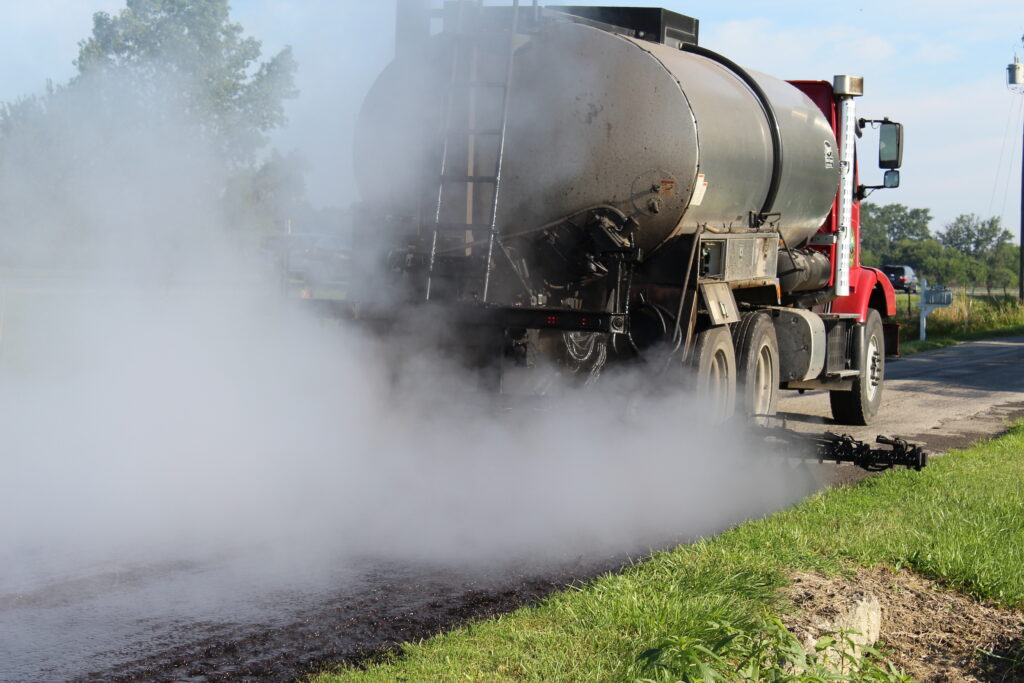
Directly behind the distributor is the chip spreader. The chip spreader applies a specified rate of aggregate onto the AE-90S. The haul trucks hook up to the back of the chip spreader to supply the aggregate and follow behind the chip spreader. While following, the haul trucks stagger helps with the compaction of the aggregate into the AE-90S. In-between the haul trucks, the rubber tire rollers embed the aggregate into the asphalt emulsion. After the chip seal has been rolled, traffic is released.
This project was a double seal (two layers of chip seal). A #9 limestone was used for the first layer and a #11 crushed gravel was used for the second, final layer. Aggregate selection can be dictated by logistics (what is available), historical performance, and other characteristics (cleanliness, hardness, etc.).
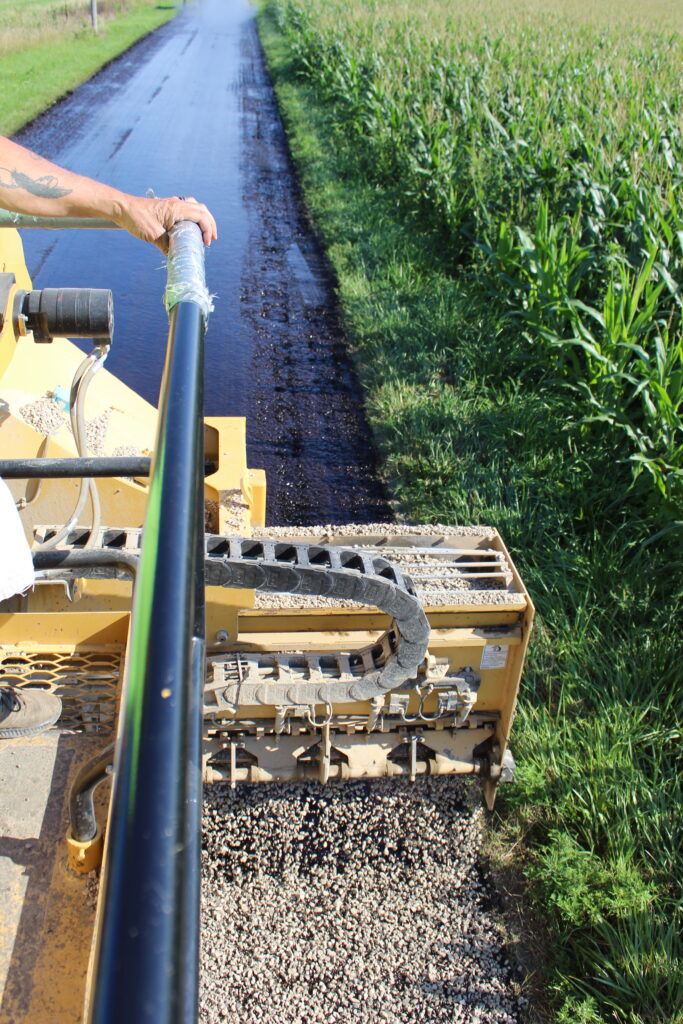
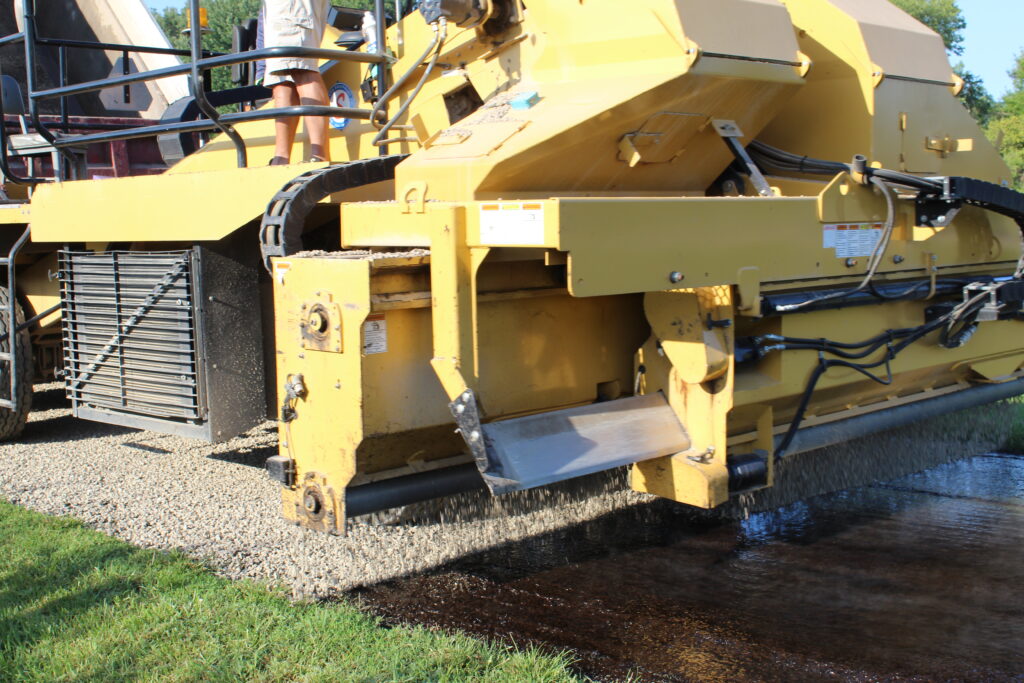
The equipment used on this project included an asphalt distributor, (with the appropriate nozzles to achieve an optimum application rate), a chip spreader, two pneumatic rubber tire rollers, haul trucks (for this project, tandem trucks), and a road broom/sweeper.
After the project is completed, the sweeper/road broom will go over the pavement to kick off any loose aggregate, if needed. Depending on the project, the chip seal will then be fog sealed.
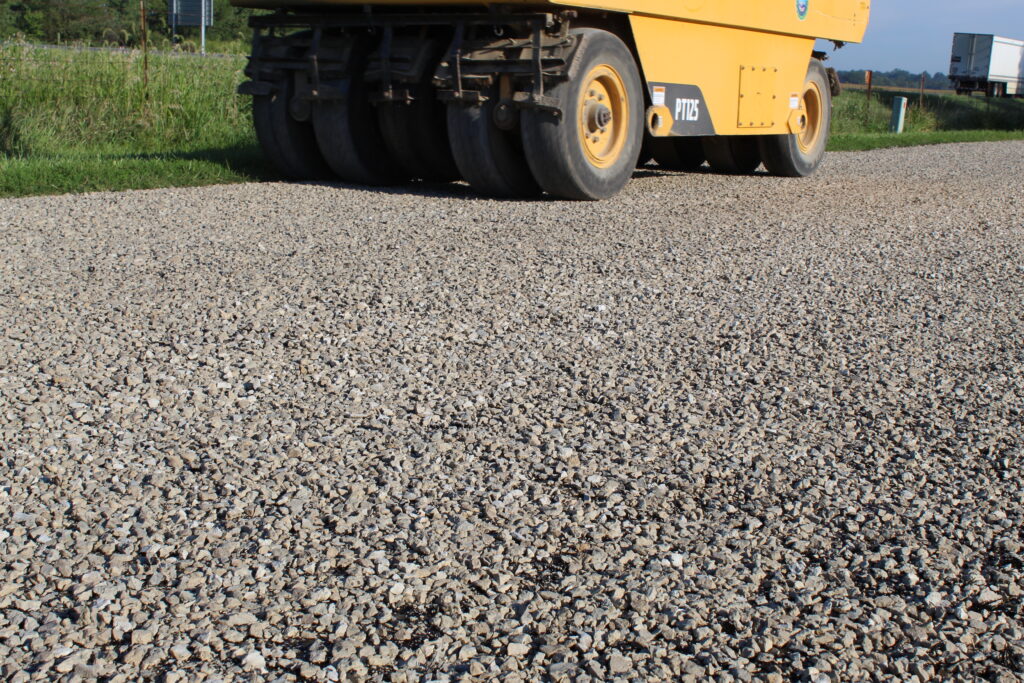
A chip seal, or double seal in this example, is a cost-effective approach to extending pavement life by sealing the pavement to not allow water intrusion, fill small cracks, and protect the underlying bituminous material from oxidation. Double seals can be effective for chip seal candidate roadways with lower PASER ratings and are more distressed.
Furthermore, there is minimal disruption to the traveling public and a quick release to traffic. It also adds an abundance of texture to the roadway, adding skid resistance, to keep the traveling public safe.
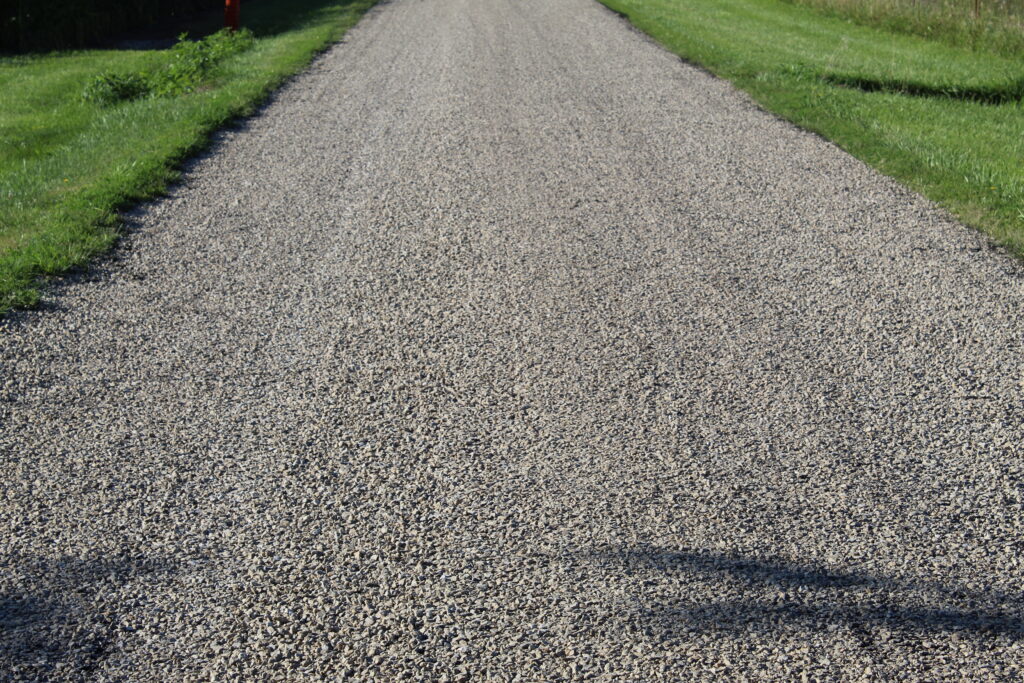
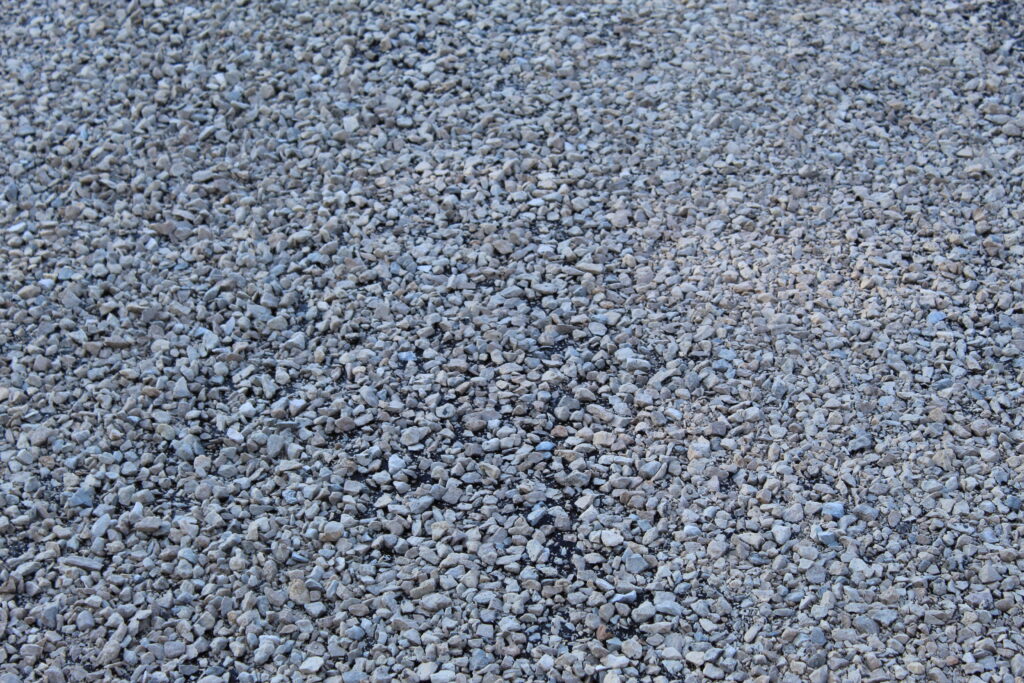
Recent Comments