Safety is an important part of everything we do. At Asphalt Materials, Inc. we understand that to succeed, we need to create a culture where everyone can share ideas and have a voice at every level of our company. Through communication, education and prevention, we accomplish our goal of getting our employees and associates home safely at the end of each day.
Our Plants
One important part of our educational training is our yearly operational audits. These audits are intended to diagnose which areas need attention and to safeguard assets by averting potential future risks and leveraging best practices.
Our team rotates between the west, central and east regions each year and targets three plants within that one region.
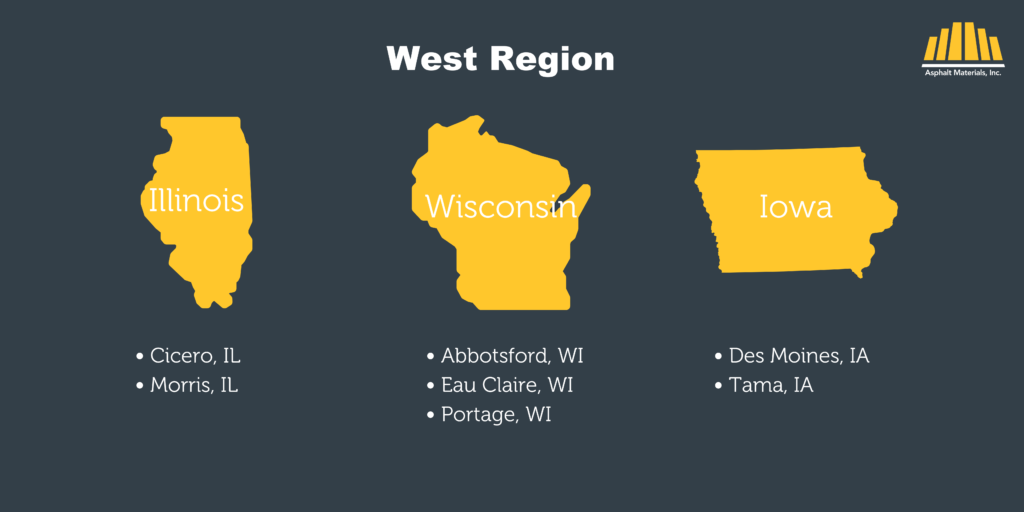
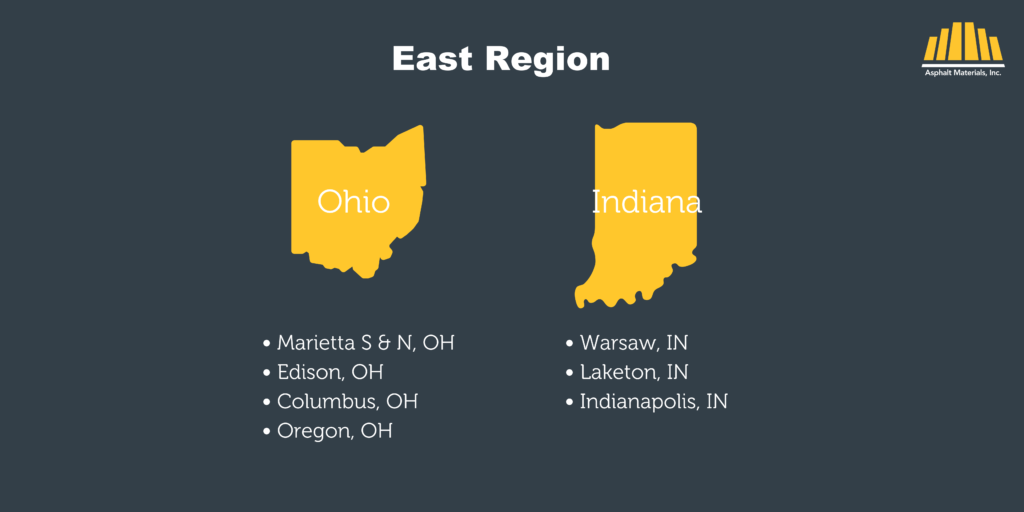
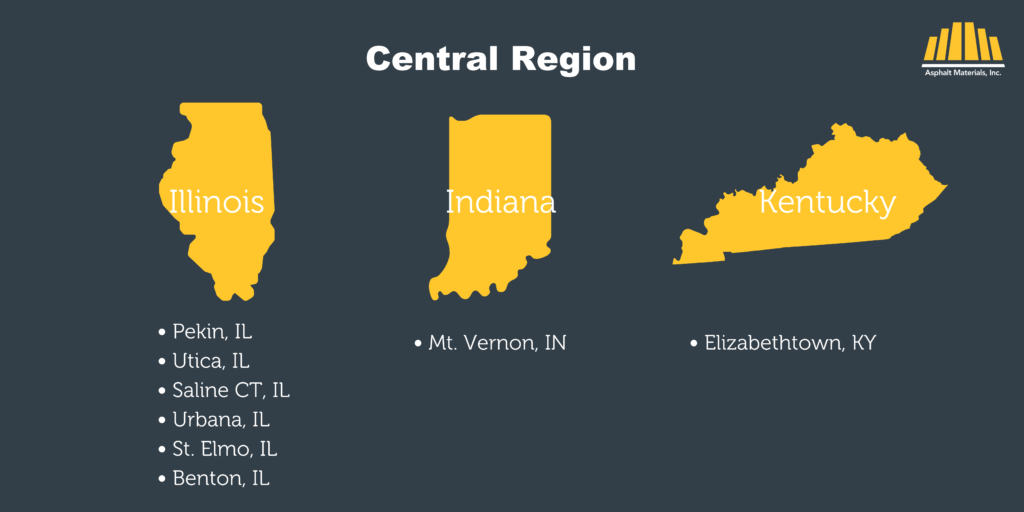
This past year our team focused on our east region and held operational audits at the Laketon, Warsaw, and Oregon plants. Team members from across our sister companies joined the operational audits to share their perspectives and collaborate on best practices, including US Aggregates Safety Manager Eric Reno and Safety and Health Representative Shayla Meinders.
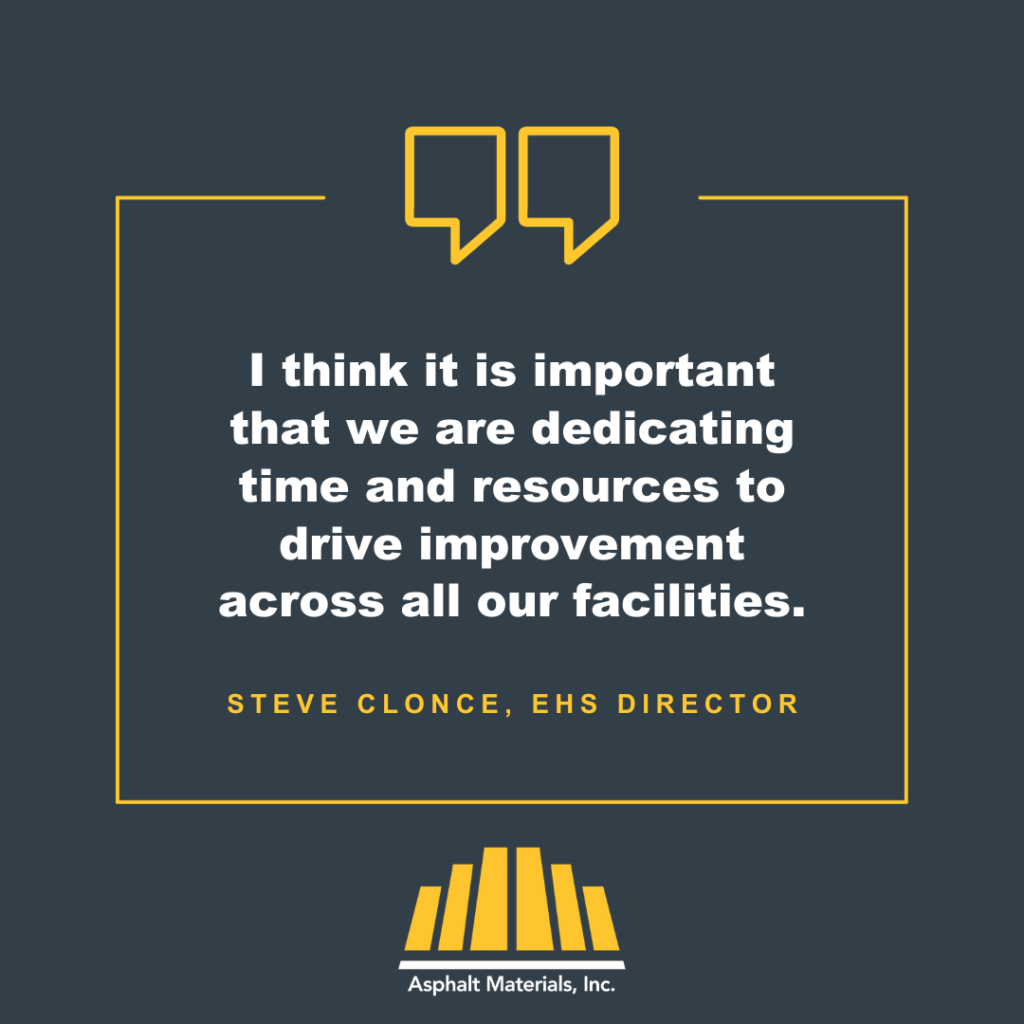
Site Audit Pro
When conducting our audits, our team utilizes an app called Site Audit Pro, which helps identify issues throughout the facility more efficiently compared to hand-written notes.
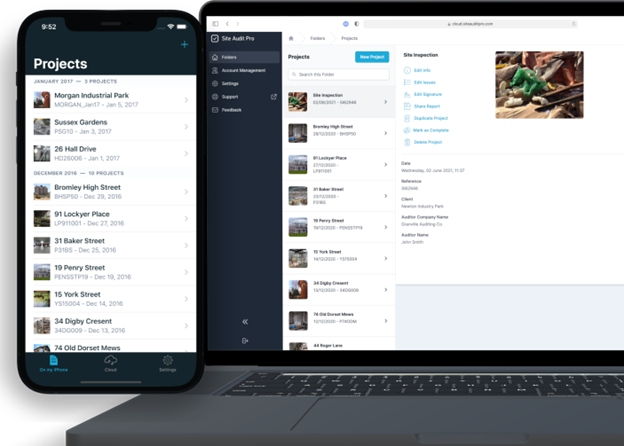
Within the app you can create projects, record issues, annotate photos and sign off on your projects. Team members are then able to record issues or best practices they notice with a photo and add a title and comments. At the end of each audit, the members can export this information and easily present it to the rest of the team.
Not only do these audits help identify and solve issues, but they also help bring best practices to other facility sites.
Best Practices
Below are some best practices recently identified and implemented for some of our plants due to recent operational audits.
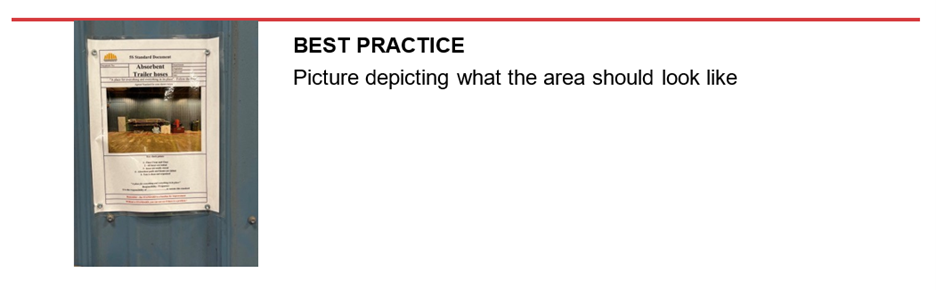
One best practice that has been implemented within our plants is the posting of photos throughout to showcase how the newly arranged area should look like. This helps maintain a sustainable process and create better efficiency throughout.
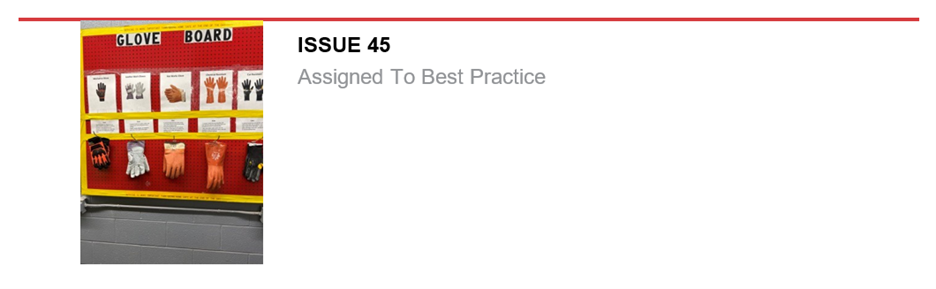
Earlier this year our safety team organized a glove board training which is showcased within this picture. You can find similar boards throughout all facilities. This allows employees to better understand the use and purpose of each type of glove.
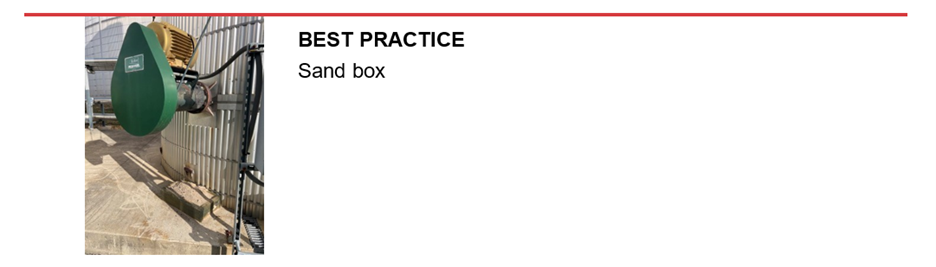
At our Laketon, Indiana, plant our team installed a sand box to catch leaks from our mixer shaft and allow for easy clean up without any spill hitting the ground.
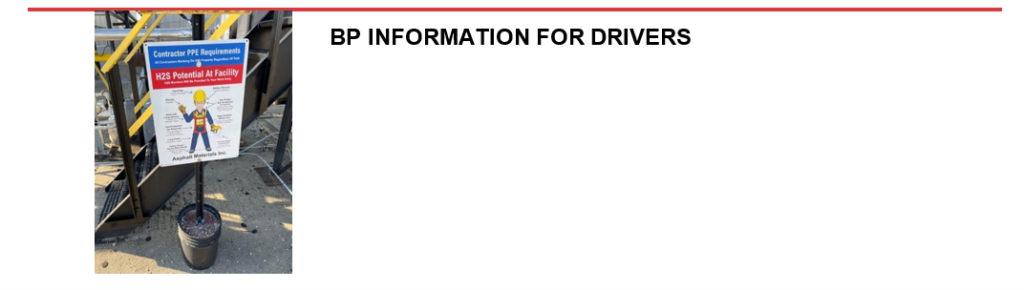
At our Warsaw, Indiana, plant the team installed better informational signs about loading and unloading, required PPE and hazard mitigation for each of their tasks.
AMI is dedicated to the safety and well-being of all our employees. That is why we continuously look for improvements and implement best practices to be shared throughout.
Looking forward, we have a lot of exciting safety programs, training and summits coming up next year. Our annual Safety Summit is being held February 29-March 1. In April we will also be launching a Safety Audits program. Keep an eye out for more information!
Recent Comments