Agencies are seeking cost-effective and sustainable solutions to make roads last longer. This is why the Heritage Research Group (HRG), Asphalt Materials Inc. (AMI), Milestone Contractors, and US Aggregates are all working together in a One HC+M project to figure out how to make the strongest, most sustainable, and cost-efficient asphalt mix in the Midwest region. One solution the team has found that is not only cost efficient, but sustainable and durable, is Cold-Construction Asphalt Pavement (CCAP®).
CCAP is a cold mix asphalt made from a blend of crushed aggregate and gelled asphalt. The gel-like structure within asphalt branches out and connects to itself, allowing the material to maintain shape. This honeycomb-like structure gives the material strength and flexibility surrounding the aggregate. The cold mix can be stockpiled for weeks or up to a few months and placed using a paver for road repair such as patching potholes or adding a new layer to low-volume roads.
“The gelled asphalt allows for an increased film thickness on the aggregate, helping to extend the ageing process,” said AMI Indianapolis sales representative Nate Jenkins. “CCAP is stiff enough to carry loads and is flexible enough to mitigate reflective cracking, is resilient to thermal cracking, and crack resistant in cold temperatures. It’s strong, durable, flexible, and is easily maintained.”
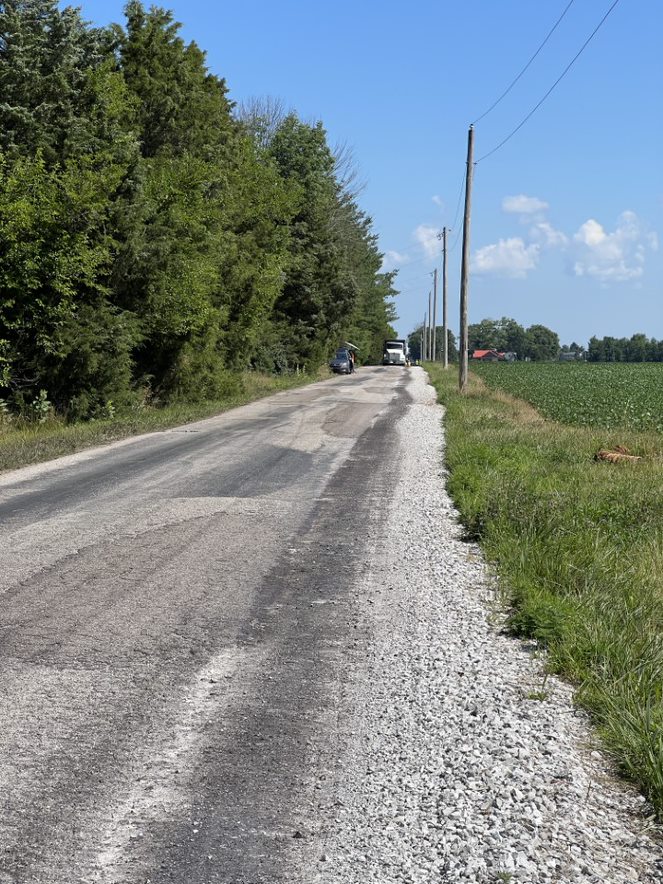
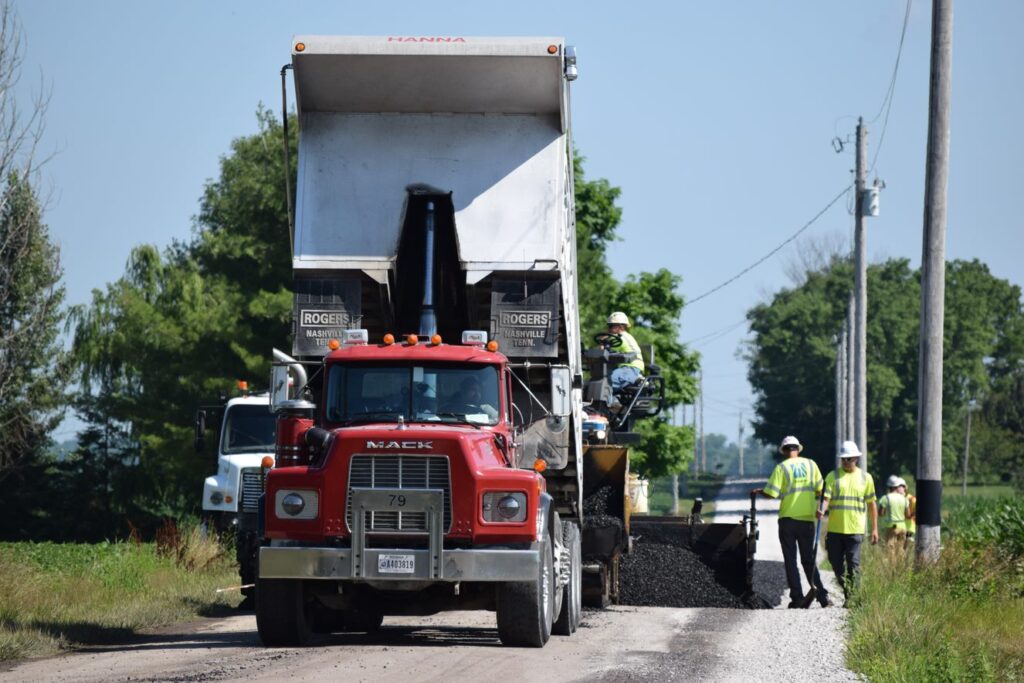
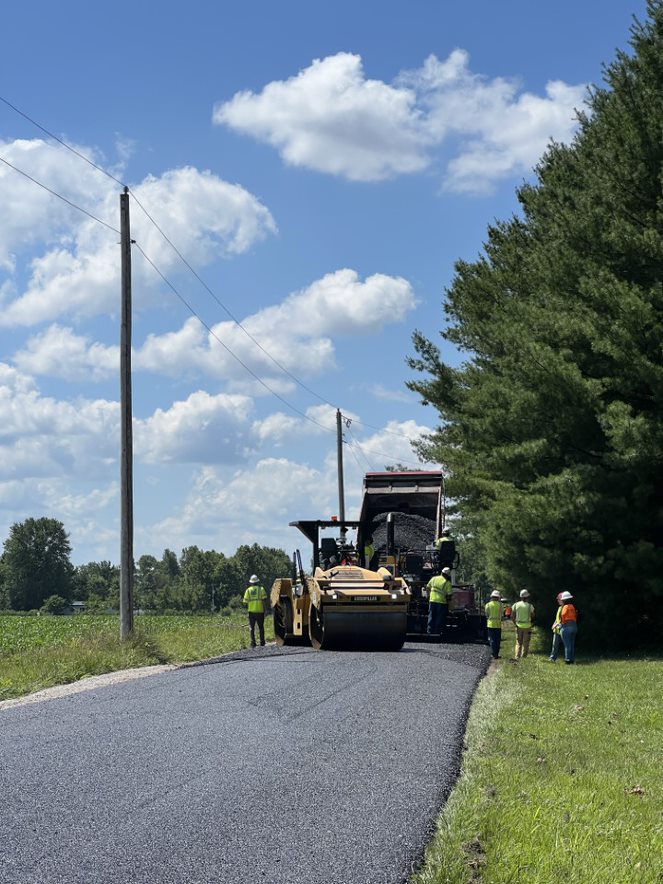
Nate and his team recently worked with US Aggregate Plant Manager Rachel Lockhart to produce CCAP for a project in Morgan County, Indiana. The CM-150 gelled asphalt was produced at the Indianapolis AMI plant, and an AMI pugmill mixed the modified asphalt with virgin limestone aggregate at US Aggregates’ 243 Quarry in Cloverdale, Indiana. The pugmill system allows a set amount of asphalt binder to combine with the aggregate. The mixing is performed at ambient temperatures, resulting in low emissions and reduced energy consumption, making CCAP a very sustainable option for agencies.
CCAP has successfully been used on roadways that are too weakened for other treatments, and it has proven itself to be more time efficient and reduce budget dollars without sacrificing structural integrity. Because the mixture is cold constructed, it is not necessary to reheat the material to elevated temperatures. The finished CCAP® mixture is then loaded and delivered to the paving site or stockpiled until ready for placement. This month, Milestone applied the mixture to Shupe Road in Morgan County.
Asphalt starts as a byproduct, and when used correctly, it can last decades because of its durability. When the road needs to be reconstructed, the asphalt and aggregate that was originally used can be reused and reapplied. Sustainable project methods like CCAP help recycling, reclamation, and leverage processes that contribute to the circular economy.
Recent Comments