Asphalt Materials, Inc. stands strong as a leader in enforcing safety protocols to protect our team from potential hazards. It is also at the forefront of sustainability improvements that enhance the health of our communities and environment. When AMI’s leadership identified a challenge that posed safety concerns and generated significant waste, the team began developing an action plan.
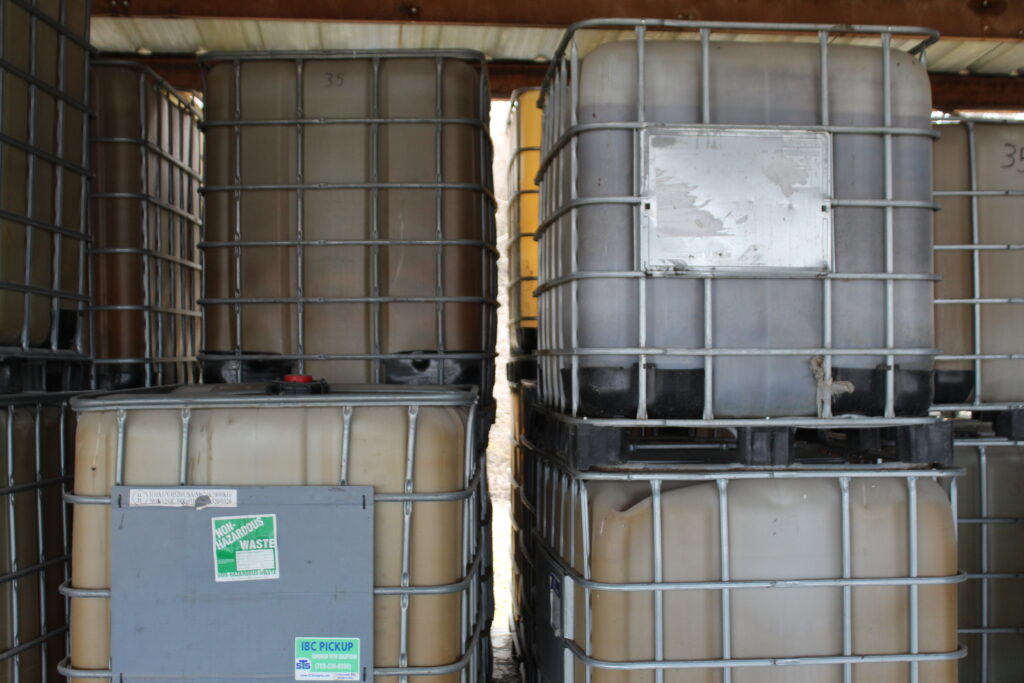
Plastic totes are used at our plant facilities to hold raw materials or waste for disposal. Once no longer needed, they would often be relocated onsite for a holding period before ending up in a landfill. This unestablished removal process presented risks to our workforce and contributed to our environmental footprint, highlighting an opportunity for improvement.
So, how did our teams tackle this challenge?
- Removing Immediate Waste
A number of these totes hold waste, presenting the highest potential for hazards to our workforce and the environment. Identifying and disposing of these totes was the easiest and most pressing step in achieving reduction goals. A cleanup at one identified site resulted in the disposal of over 400 totes. This effort not only addressed an immediate waste issue but also revealed the need for a new standardized process of managing and disposing of waste company wide.
- Minimizing Areas of Use
Our operations team approached this task by exploring various possibilities to eliminate the use of totes wherever feasible, such as adding chemical tanks and relocating raw materials from totes to bags. Each plant produces different materials and requires individual solutions. Regional directors worked to collect data for each site and collaborate with plant managers to identify feasible solutions for their locations. For example, they identified an opportunity to make updates to our Morris plant which will yield a reduction of 200+ totes while improving operational efficiency.
- Redistributing Inventory
The remaining totes led our continuous improvement department to investigate ways to consume inventory, particularly that labeled as “slow-moving” or “stale”. Collecting data and analyzing consumption as a network allowed us to leverage database platforms for better visibility of inventory at all sites. If a facility needs material, it can now reference this database for existing inventory across locations, as well as the usage rate of any given material per location, to determine potential excess. By redistributing materials between sites rather than purchasing new, the team ensured that resources were utilized effectively, minimizing overall material waste. This alone led to substantial inventory savings.
The team set a goal to reduce the tote count by 80%, starting with a baseline count of 1159 totes in 2023.
Through disposal, redistribution and consolidation at all facilities, they have significantly reduced the number of totes throughout our network, surpassing the initial goal and boasting an 82% reduction as of 2024.
Although our initial goal is achieved, the work continues! Operations is always looking for opportunities to reduce waste at our sites. Teams are encouraged to share areas of potential improvement and with a new process in place, departments can work together to implement innovative solutions.
How a LEAN Mindset Pushes Us Forward
AMI works toward process improvement across business functions with the expertise of our continuous improvement team at the helm. This team has taken the company on a journey to LEAN, a philosophy centered around eliminating waste and streamlining processes to maximize efficiency and value.
Originating from early manufacturing production methods in the 20th century, LEAN is a methodology that focuses on creating efficient workflows and delivering high-quality outcomes. In practice, LEAN processes emphasize the importance of reducing the 8 types of waste when possible: transportation, overproduction, waiting, inventory, skill, defects, overprocessing and motion.
From a LEAN perspective, the reduction of totes has been transformative. The two largest benefits that the company gains are improved site conditions and the implementation of a standard process to maintain these improvements.
By Joining Forces, We Can Go Further
The initiative to reduce plastic totes was embraced by the entire company. From the execution of totes removal to the process implementation for future work, a new path has been paved for inventory management. Most recently, a materials review board has been formed to communicate excess inventory and stale materials on a regular basis. This collaborative effort between operations, logistics, finance and more ensures that materials are redistributed effectively, reducing waste and optimizing costs.
Sustainability efforts at AMI often create domino effects. The team’s work on tote reductions has led to safer operations, quicker production, and significant cost savings, but it also sparked additional recycling opportunities, like our partnership with sister company U.S. Aggregates in reusing our pallets.
We’re building for generations, meaning we are committed to leaving our people, our planet and our communities better than we found them. Does this purpose resonate with you or someone you know? Passionate individuals are always welcome to apply to join our team. Check out our careers page to see our current opportunities.
Recent Comments