Co-authors: Andrew Eicher & Naarah Holloway
Road managers know that the longitudinal joint is the first part of the pavement to fail. As a road’s most permeable part, this joint is susceptible to the elements. Air and water work down through this gap causing the joint to deteriorate, crack and pothole. And when the longitudinal joint fails, the rest of the road soon follows—triggering the need for even more maintenance.
Centerline trench mill and fill, or slot paving, is a maintenance technique that agencies may use to isolate and repair the longitudinal joint area of a pavement. Instead of replacing the entire pavement, agencies may elect to mill out a 2- to 3-foot-wide trench, or slot, over the longitudinal joint area and fill it with new materials. Additionally using a Void Reducing Asphalt Membrane (VRAM) within this process can also more effectively seal the trench from the bottom up, reducing permeability across the trench and the two new joints. Therefore, preventing more maintenance work later down the road.
Our team recently observed the use of a VRAM with a slot paving technique on Montana Highway 200. The trench was filled with new hot-mix asphalt (HMA) and resulted in two new joints.
Project Background
A rumble strip installation in 2016 contributed to longitudinal joint failures on Montana Highway 200. This triggered the need to reconstruct over 85,000 linear feet of longitudinal joint in 2023. The Montana Department of Transportation (MDT) elected to use a trench mill and fill technique to remove and replace the joint area 2 feet wide. VRAM was applied to the width of the trench prior to paving to protect the new HMA and rumble strips that have been installed. The project will also have a full-width chip seal installed in 2024.
Project Details
- Owner: Montana Department of Transportation (MDT)
- Prime Contractor: Knife River
- Applicator: Z&Z
- VRAM Supplier: Seneca Petroleum
- Location: Montana Highway 200
- State: Montana
- County: Lewis and Clark
- Date Constructed: August 14-17, 2023.
Several personnel were present, including members from Z&Z, Lance Streeter from Knife River, Bart Lungren from Seneca, Dan Horner from Cimline, Montana DOT personnel including Harold Woodhouse, Oak Metcalfe, Chris Neuman, Luke Lindberg, and Andrew Eicher from Asphalt Materials, Inc. as an observer.
Project Summary
The first day of the project started roughly 10.3 miles west of the Lincoln city limits. Z&Z arrived on site to begin heating VRAM blocks in the MA4 kettle. Three additional kettles were used to pre-heat blacks for refilling the application equipment. During the heating, Knife River milled the centerline joint going east towards Lincoln. This was a 2-foot-wide and 1.8-inch-deep milling operation to remove and replace the existing rumble strips.
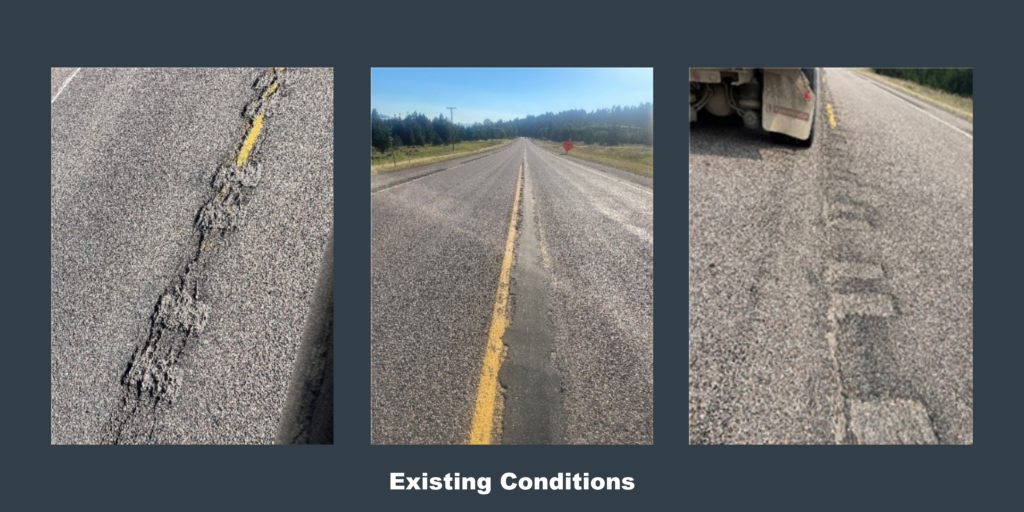
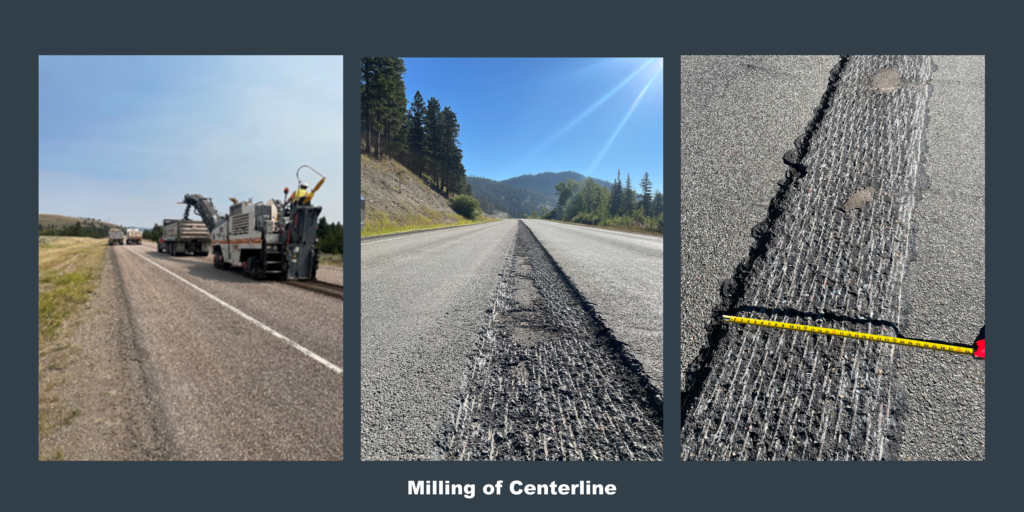
VRAM application began on the west end of the project starting with a target rate of 0.98lb/ft. This was the first application of VRAM in a trench, so the applicator was cautious to use higher rates due to concerns of confinement in the trench. The application rate would be increased over the course of the project as discussed below.
Shortly after the initial VRAM application, paving began behind the VRAM application. Paving equipment does not have to wait long to cross over the trench, as VRAM cools within minutes of application. No pickup was noticed by any of the construction vehicles on site. The mix was laid slightly wider than the trench width, matching the VRAM application. The first steel drum roller was used to compact the edges of the trench and match the existing surface. The second roller used pneumatic rear tires to compact the middle of the trench further without bridging.
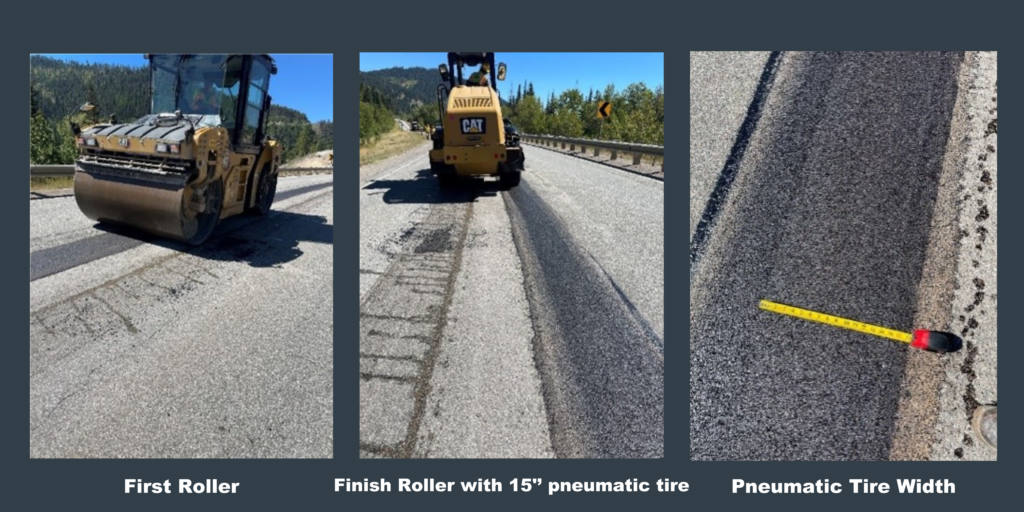
By the end of the first day approximately five miles of VRAM had been applied, and 3.9 miles had been paved. The VRAM application covered all the trench that had been milled that day.
On the second day, it was discussed to increase the VRAM application rate, as no flushing was noticed the previous day. The rate was set to start at 1.10 lb/ft. After further discussion, the rate was set to 1.15lb/ft at mile marker 74 going east. By the end of the day, the rate was set to 1.20lb/ft. Milling and VRAM application stopped for the day at the Lander’s Fork Bridge, just west of mile marker 78 on Highway 200.
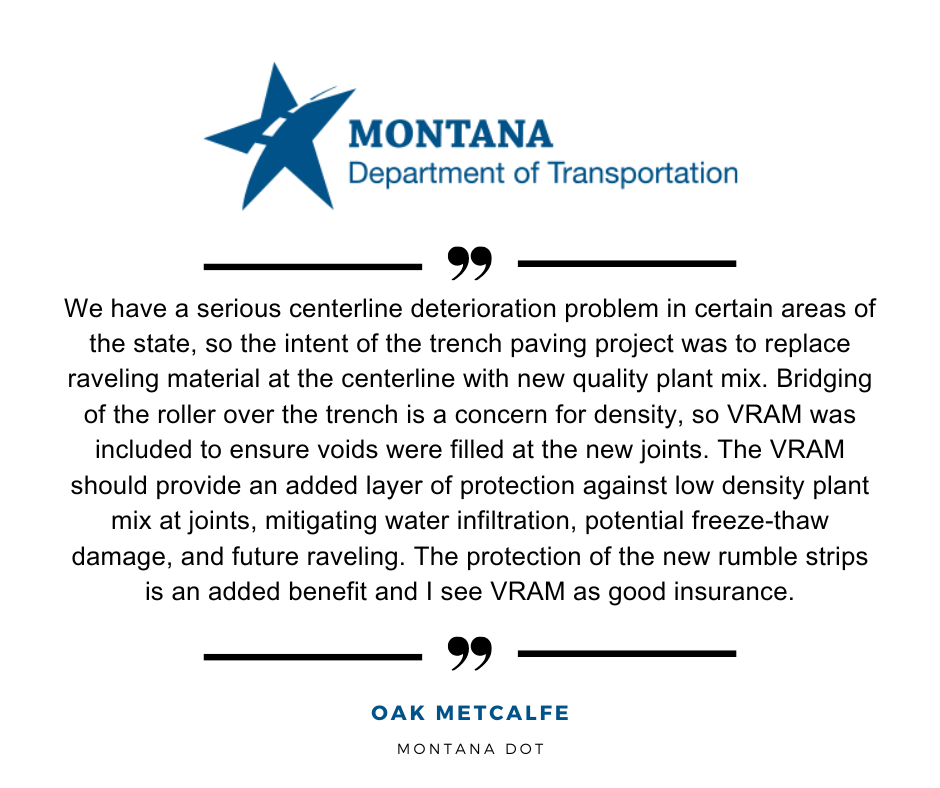
On the final project day, VRAM application started again at the Lander’s Fork Bridge continuing east. No flushing was observed the previous day, so the DOT elected to increase the application rate to 1.50 lb./ft. Several rate checks were taken around miles 78 and 79 to verify application rates.
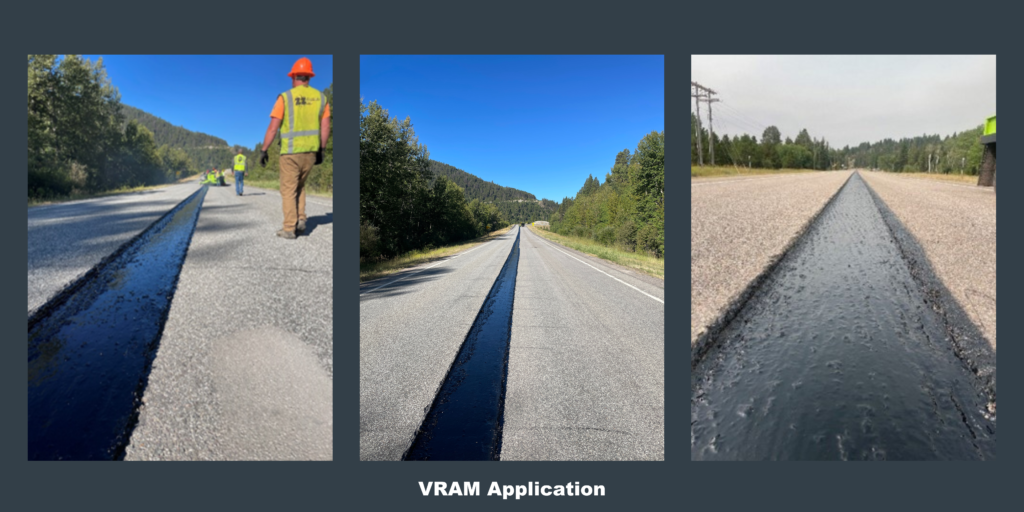
No flushing was noticed when the paving reached the higher 1.50lb/ft rate section for the remainder of the project. After some discussion with the contractor and DOT, a 97 ft. control section was marked off at mile 82 going east. This section was to be sprayed with conventional tack coat the following morning prior to the paver reaching it. This section will be used as a comparison of the VRAM to conventional trench paving practices.
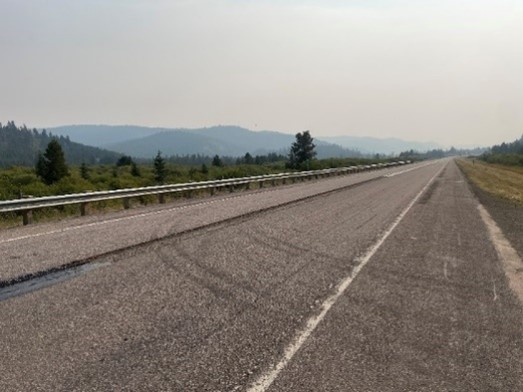
Asphalt Materials, Inc. is a supplier of a Void Reducing Asphalt membrane called J-Band®. You can learn more about our product by clicking here and explore our interactive map that showcases projects that have utilized a VRAM at the time of construction.
Our in-house R&D laboratory the Heritage Research Group, has played a big role in the creation of our products and techniques. Today, our labs provide innovative products, processes, and training to create longer-lasting, safer roads. We constantly seek new and inventive solutions by working closely with our customers and partners.
If you would like to learn more about the use of a VRAM with a slot paving technique, please reach out through our email: jbandinfo@thgrp.com
Recent Comments