Over the years, asphalt has become the most popular choice when it comes to selecting environmentally friendly pavements. To take it one step further, cold mix pavement layers have been developed to create even more sustainable products for road construction. Cold recycling techniques are methods that not only avoid the application of heat but reuse aged asphalt pavements already within the current infrastructure. This technique used helps treat raveling, potholes, skid resistance, rutting, block cracking, and so much more.
Cold recycling includes two subcategories, cold in place recycling (CIR) and cold central plant recycling (CCPR). In this article we will highlight a successful CIR project in Jefferson County, Indiana.
Jefferson County Project
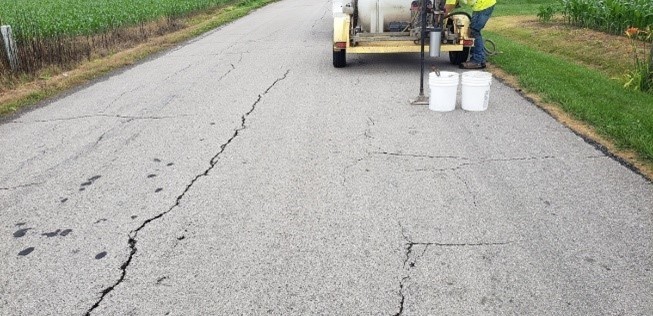
Jackson Road is a 2.2-mile road connected to Indiana State Route 62. The county asked the Heritage Research Group (HRG) to perform a pavement investigation to examine material types and measure pavement thicknesses. After research was conducted, HRG concluded that Jackson Road needed more than just conventional repairs.
The existing pavement on the road was experiencing age-related cracking. Stripping and debonding were also observed in the existing asphalt, reaching as deep as five inches from the surface. The traditional solution to fix these issues by milling and filing a depth of five inches was not a cost-efficient option for Jefferson County. The county was looking for a solution that would save money at the time of the project and in the future.
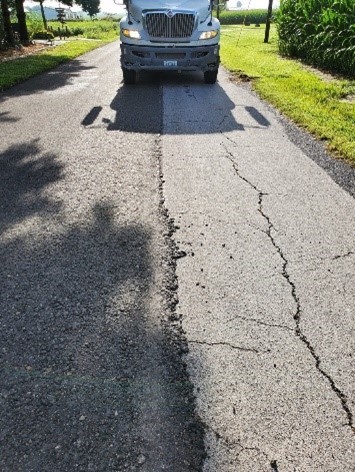
Solution
The CIR process was introduced to the county to help solve deterioration and save funds. The process uses pre-existing material that the county already had and an asphalt emulsion to create a new pavement layer.
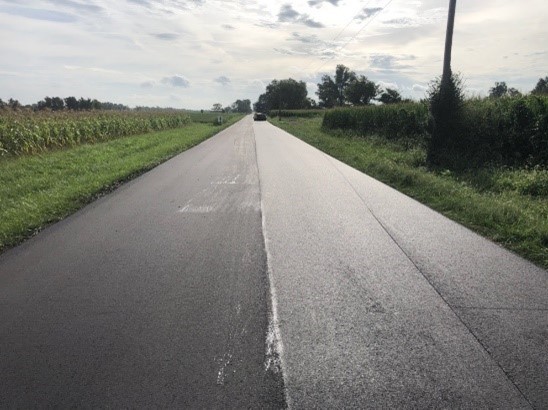
The CIR process, performed by Dunn Company, began with pulverization of five inches of distressed asphalt pavement along with an injection of engineered emulsion at a specified rate. The injected mixture was then placed and compacted back onto the underlying pavement layers. Using CIR to rehabilitate the existing pavement took two production days. Once the CIR lift was finished curing, a 1.5-inch HMA surface was placed.
Conclusion
The Heritage Research Group concluded that using CIR for this project had an initial cost savings of more than $200,000 when compared to a mill and fill of five inches of HMA. This equates to total savings of approximately 47% of the final project cost. The CIR process recycled 7,000 tons of existing asphalt pavement, while eight trucks of new material were delivered to the project site. The project took place in the summer of 2020, and was the first project to utilize CIR in this region of Indiana.
Sources
NCAT. (2018). Cold recycling of Asphalt Pavements. Samuel Ginn College of Engineering. https://www.eng.auburn.edu/research/centers/ncat/newsroom/2018-spring/coldrecycling.html#:~:text=As%20its%20name%20implies%2C%20cold,non%2Drenewable%20resources%20and%20energy.
Public Works. (2023). Cold in-place recycling (CIR). Department of Public Works. https://dpw.lacounty.gov/gmed/lacroads/treatmentcoldinplace.aspx
Brown, D. (2020). Success story. PPRA. https://roadresource.org/resources/100/success
Recent Comments