At Asphalt Materials, Inc. (AMI) safety is a part of everything that we do. We are continuously trying to find innovative ways to help our employees get home safely each day, including by implementing plant automation systems in all our facilities across the Midwest.
Automation-focused capital projects started in 2018 and will continue through 2026. Plant-critical processes that have received automation upgrades include polymer milling, emulsion milling, truck loading and more.
Plant automation plays a pivotal role in enhancing both efficiency and safety within our asphalt plants. By automating repetitive tasks and processes, we can significantly increase productivity. Additionally, with automation, we can enhance safety by minimizing workers’ direct contact with potentially hazardous machinery and materials.
The integration of automation technology streamlines operations and prioritizes the well-being of workers.
Polymer & Emulsion Milling
Polymer milling and emulsion milling are two of the most important processes being automated at our plants. Prior to installing automation, the system that fed the materials happened through manual action by the operator. They had to open valves, regulate the flow of pumps and be exact with the quantities being produced. The new automation system installed has a processor that has logistical steps programmed into the technology that allows the operator to select specific recipes, manipulate operating conditions, and help minimize variation during production, therefore improving product consistency.
The biggest benefit of integrating these systems is increasing the safety of our operators. Prior to automation, the operator’s focus was split between multiple process indicators spread out across the production area. However, now with an automated controls system in place, the operator’s process conditions are all centrally located, giving the operator increased confidence and time to adjust in the event of an out of tolerance condition.
Several of our locations have implemented this milling automation including our locations in Edison, OH, Des Moines, IA, Morris, IL, Indianapolis, IN and more.
Below you will find before and after pictures of emulsion mill automation being installed at our Indianapolis plant.
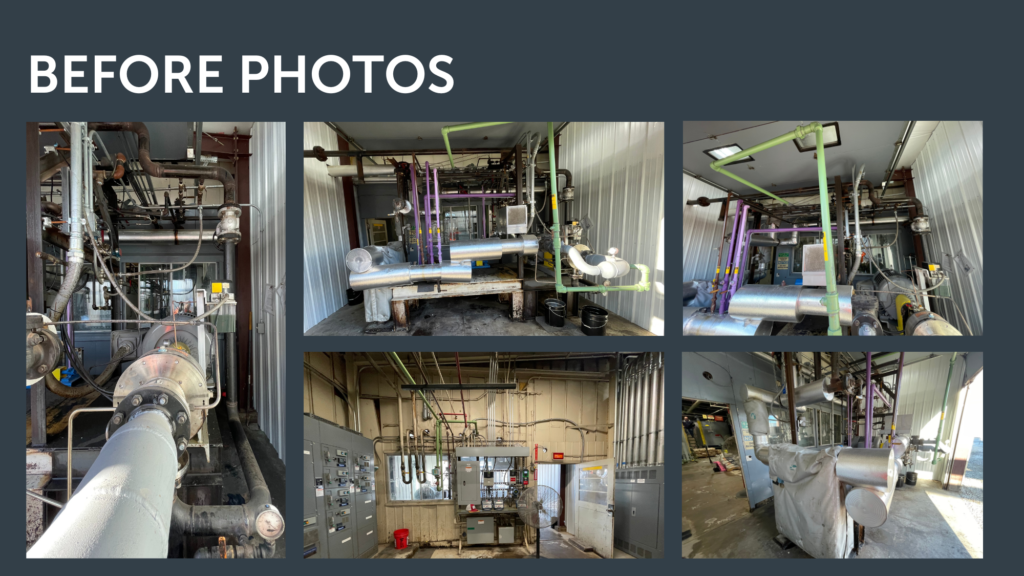
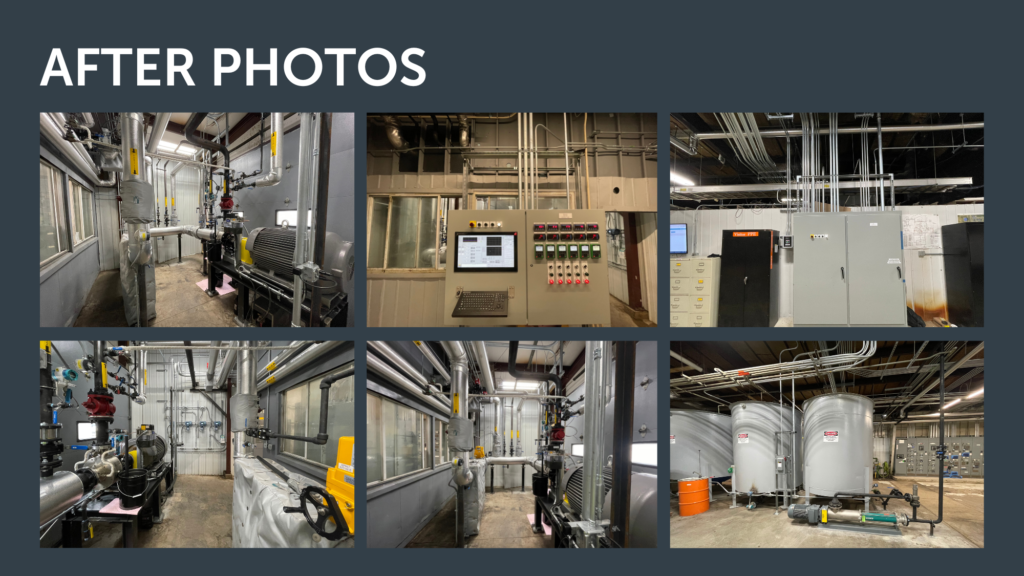
Truck Loading
Drivers who pick up products at our plants must drive up on a scale and have an AMI operator affirm the product selected and assist in the spouting and loading of the truck. This adds time to the load-out process and puts AMI operators at a position of increased risk at the top of a truck.
After implementing an automated loading system, drivers no longer must interact with an additional operator. They can drive up on the scale and press a couple buttons to select their material and drive off, which helps to expedite truck traffic at facilities and improve the safety conditions for our plant personnel.
Several of our locations have implemented this including Marietta N., OH, Mt. Vernon, IN and Cicero, IL.
The integration of plant automation has revolutionized operations by significantly enhancing both safety and efficiency amongst our plants. By reducing variation in our processes, we can ensure we produce a more consistent product for our customers and provide a safe working environment for our employees. We look forward to sharing future automation being integrated into our plants throughout the next couple of years.
Recent Comments