An excerpt from the American Road & Transportation Builders Association (ARTBA)’s July/August 2023 Transportation Builder issue.
Have you ever heard the expression, “A chain is no stronger than its weakest link?” The adage can be applied to road construction. No matter how strong and durable your materials, if one component is breakable, the rest are compromised as well.
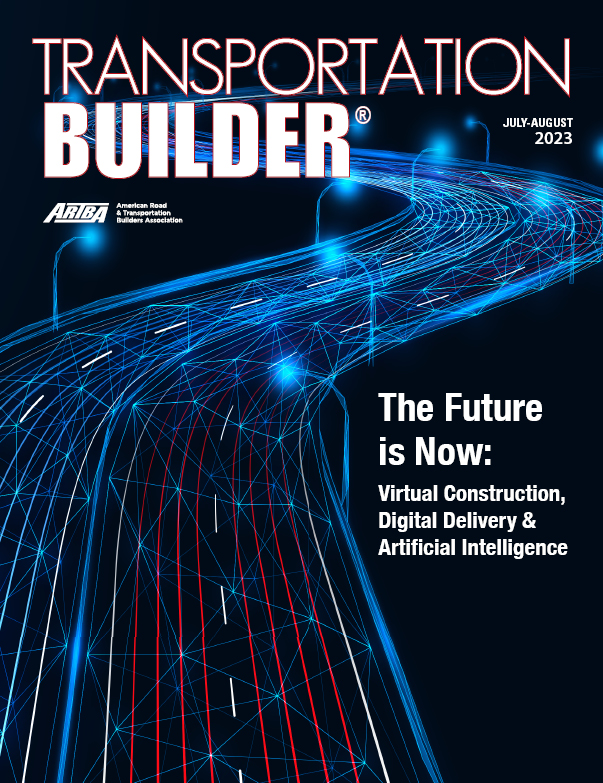
In roadways that link, the longitudinal joints often have a history of deteriorating much quicker than the road surface itself, creating potentially dangerous situations for drivers and reducing the lifespan of pavement.
Damage to joints occurs when a fresh batch of hot-mix asphalt (HMA) is laid adjacent to an existing lane. Most often, differences in temperature and mat plasticity cause improper bonding of the fresh HMA with the older asphalt lane. As a result, the longitudinal joint is significantly less dense than the rest of the pavement. Over time, a crack occurs between the mats, allowing air and water to seep in.
An Ounce of Prevention
To build longer-lasting roads, innovative solutions have been developed to reduce permeability at the longitudinal joint. Research shows that using a Void Reducing Asphalt Membrane (VRAM) and a Rapid Penetrating Emulsion (RPE) at the centerline can significantly extend pavement life.
VRAM is a specially formulated polymer modified asphalt membrane applied at the time of construction, before the hot mix asphalt is put down. VRAM migrates upward into the HMA and fills voids. As voids and connected voids are filled, permeability decreases, and this protects the pavement, extending the life of pavement an additional 3-5 years.
While VRAM fills voids from the bottom up, RPE is applied on the surface. Instead of sitting on top of a pavement like traditional fog seals, RPE is a specially formulated emulsion made to penetrate quickly down into the asphalt surface. The emulsion carries additional asphalt residue into the smaller interconnected voids of the pavement. Voids near the surface are filled (top – down), which reduces permeability.
While VRAM and RPE have significant benefits on their own, they create even stronger roads when used together, and in turn have long-term economic, social, and environmental benefits.
Better Together
The longitudinal joint is not only the most vulnerable part of the pavement, but it is also the most expensive part of the road. The centerline of roadways often contains rumble strips, pavement striping and/or reflective pavement markers (RPMs) to keep drivers safe. When the center of the road deteriorates, these costly safety measures must be repaired or replaced. Agencies that invest in innovative joint-protecting technologies like VRAM, have seen roads that last up to five years longer and typically deliver a return on investment of three to five times its cost.
The use of both RPE and VRAM has been especially beneficial on roads featuring centerline rumble strips (CLRS). More and more transportation departments are investing in CLRS to warn drivers that they are straying from their lane. While CLRS are an investment to save lives, these textured grooves are milled into the pavement, increasing permeability. Applying VRAM at the time of construction, under the surface where centerline rumble strips are installed, reduces permeability in this critical area. During post-construction, it is recommended to use RPE as a preventative and remedial treatment for longitudinal joints. When these solutions work together, there is increased protection for roads and drivers.
Proper application of these innovative technologies will improve asphalt pavement service life. A pavement with a longer service life can also significantly increase pavement sustainability as well. When longitudinal joints last longer, roads last longer, drivers have smoother, safer rides, and agency resources go further.
Read the full July/August 2023 Transportation Builder issue here.
Recent Comments