AMI is committed to changing the standard in the asphalt industry. Our companies strive to implement new processes, ideas, services, and products with the goal of creating a more effective solution to your road construction projects. Our dedication to quality often results in improving roads through the process of pavement rehabilitation. Each project contains different conditions and construction histories which may alter the approach to conducting pavement rehabilitation, but there are several processes that can be utilized upon reviewing a pavement individually. In general, pavement rehabilitation is suited for pavement in the C, D and F pavement condition zones. This article will address how and when each process is used.
The processes reviewed here include the following:
- Mill & Fill: This entails removing the existing surface layer with a milling machine and then transporting the material to a storage facility. New asphalt is then used to ‘fill’ the area that was milled. This allows for upwards of seven-to-10 years of additional durability. This process is faster than a full reconstruction, reducing costs by saving time as well as materials.
- Mill & Fill with Patching: Similar to mill & fill, this process is used to address localized pavement issues and eliminate distress from damaging new overlays. This option is efficient for time but can be costly.
- Pavement Recycling: This process manifests itself in three separate subcategories:
- Full Depth Reclamation (FDR): Maintains a typical depth of 5-12 inches and emulsified/foamed asphalt or Portland cement acts as its stabilizer. This is often used as an alternative to reconstruction.
- Cold In-Place Recycling (CIR): Maintains a typical depth of 3-5 inches and emulsified/foamed asphalt acts as its stabilizer. This is often used as an alternate to deeper mill and fill, or as an alternative to partial depth patching.
- Cold Central Plant Recycle (CCPR): Maintains a typical depth of 3-6 inches and emulsified/foamed asphalt acts as its stabilizer. This is often used to create a structural base layer.
As we take a deeper look at Cold In-place Recycling, it is important to address the advantages and challenges that accompany the process.
Advantages to Cold In-Place Recycling:
- Engineered Process: Calibrated equipment performing recycling to state DOT specifications with engineered materials (INDOT Section 416 as an example).
- Cost Efficient: Significant cost savings can be realized by agencies on projects.
- Advantage for Driving Public: Significant reduction in trucking to and from a roadway.
- Environmental Benefits: Reduced demand for virgin materials.
Challenges to Cold In-Place Recycling:
- Seasonal: Seasonal application times are required to accommodate strength development of the material
- Surfacing: Recycle layers are not intended to be surface layers
- Curing: Time delay until overlay is installed on the recycled mat; during this time, carrying live traffic
- Thickness Limitation: Recommended maximum final compacted thickness is 5 inches.
Below is a visual example of a Cold In-Place Recycling Success Story
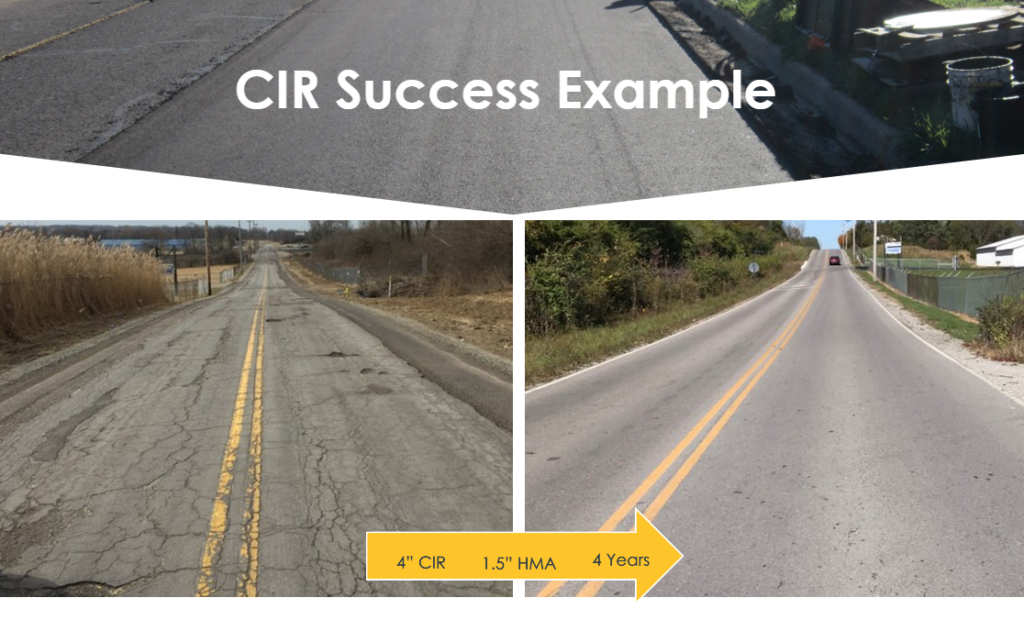
After understanding the advantages and limitations of Cold In-Place Recycling, the next question to address is how to fix the deeper problems. Such cases may require full depth reclamation (FDR).
Full Depth Reclamation comes in 3 forms:
- Mechanical: pulverize, shape and compact.
- Bituminous – Emulsion: pulverize, shape – inject, stabilize compact.
- Chemical: pulverize, shape – spread, mix, stabilize, compact.
Now, we compare and address both the advantages and challenges that inevitably accompany full depth reclamation.
Advantages to Full Depth Reclamation:
- Engineered Process: Calibrated equipment performing recycling to state DOT specifications with engineered materials
- Cost Savings: Significant cost savings can be realized by agencies compared to reconstruction and rehabilitation with significant amounts of patching
- Versatility: Treatment depth and materials selected around critical pavement issues that needs addressed
- Environmental Benefits: Reduced demand for virgin materials, eliminates remove and replace
Challenges to Full Depth Reclamation:
- Multi-Step: Create more time in the pavement rehabilitation cycle than CIR, but far more efficient than remove and replace
- Surfacing: Recycle layers are not intended to be surface layers
- Curing: Curing can vary across the categories of Full Depth Reclamation
- Thickness Limitation: Recommended minimum final compacted thickness is 5 inches (typically using emulsion); For perspective, the INDOT maximum reclamation depth is 10 inches
Below is a visual representation of each equipment step during injection of a Full Depth Reclamation project
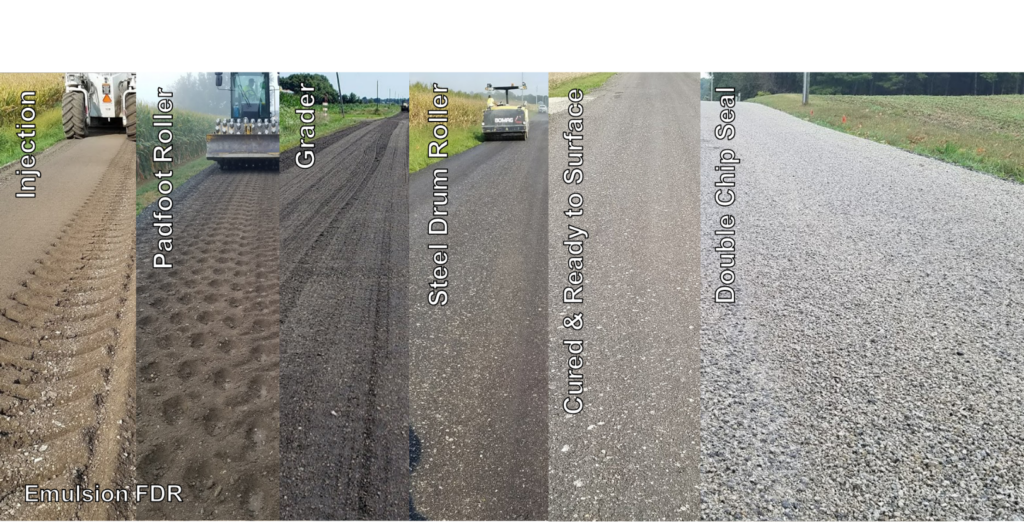
Now, we address the question, “If the recycle treatments require a wearing surface, what can be used?” Below, there’s an image that outlines both high and low volume surface options.
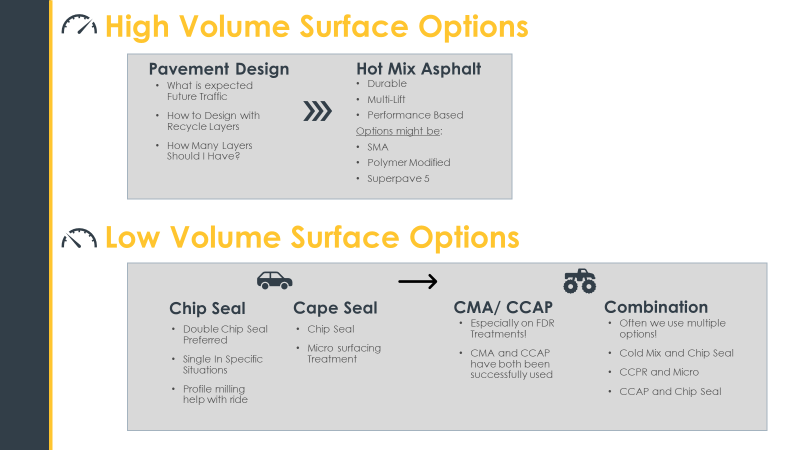
To learn more, you may contact Jason Wielinski, P.E. at The Heritage Research Group via email at: jason.wielinski@hrglab.com
Recent Comments