Any business that has been around for over 65 years should have a strong commitment to innovation. Asphalt Materials is that company. Our teams are focused on helping build longer-lasting, safer roads. To do that, we focus on big challenges as creative problem solvers. We have a unique opportunity available to us and our customers in that we are part of The Heritage Group, which includes the expertise that resides within The Heritage Research Group.
Collaboration is a hallmark of our approach as well. Working with contractors and departments of transportation, we take a collective approach that fosters long-term relationships and mutual trust. A recent project created an opportunity with Indiana State Road 234. The construction project consisted of 126,505 square yards of Cold In-place Recycling (CIR) at a depth of 4-inches. The project length was 10.37 miles with a 22 foot width. The project progression can be seen in the image below.
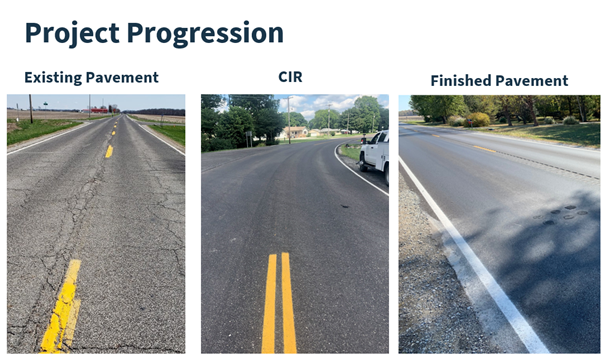
While comprised of similar components to conventional Hot Mix Asphalt, CIR lifts cannot be sampled in the same way to measure and confirm quality of the material. Instead, each CIR candidate pavement is sampled, with the representative materials going through a mix design process designed to closely approximate the CIR construction procedure in the lab. Once the CIR mixture meets or exceeds specified laboratory standards, construction can begin.
Per industry standard, several tests are performed during CIR operations to verify the exact material quantities are added to the mixture per the project’s mix design. In-place density testing is also performed to confirm optimal compaction is reached throughout the placed CIR lift. While this testing method is rigorous for the mixture’s components it does not directly measure mixture performance. The current testing standard reveals opportunities to test the constructed material for performance that is timely from a construction perspective and valuable for agency and contractor customers.
Heritage Research Group designed a field sampling method to sample constructed CIR materials just prior to field compaction, allowing for test specimens to be produced and performance tested, similar to mix design test specimens in the lab.
Additionally, a rare opportunity arose to sample the CIR by coring, shortly after construction and the final HMA overlay was completed. This provided field cores from the project for further analysis that is truly representative of the mixture.
Six, 6-inch cores were collected from eight locations on the project (see example below).
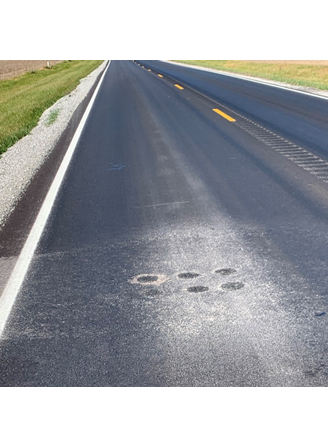
Based on these testing and material sampling opportunities, a research project was formed as follows:
- Evaluate sampling procedure for field-collected samples.
- Compare mix design results to field-collected samples.
- Quantify impact of delayed compaction of field samples.
- Compare mix design, field samples to field cores.
The variation in approximated versus representative processes in the three types of CIR samples provide a unique perspective to confirm accuracy of the field sampled mix tests and of the initial mix design test results. A diagram outlining the differentiations between mix design, field samples and field cores can be viewed below.
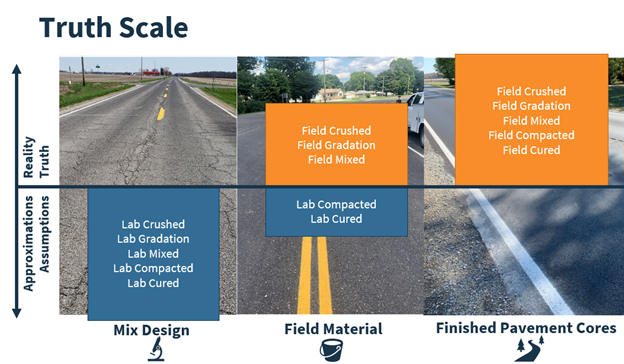
All of the CIR processes are approximated in the lab to produce a mix design, while field sampled materials contain more accurate versions of these processes because they are sampled from the constructed lift. Finally, cores collected from the project, several months after the CIR was completed, provide the most accurate version of the mixture, all of the CIR processes, including compaction, being true to the constructed CIR.
After conducting testing to determine air voids in the mixtures, specimens were tested for marshall stability and indirect tensile strength in dry and wet conditions. These results are used to estimate a mixture’s resistance to water damage, rutting, and cracking in tension.
To further understand the long-term performance of the mixture, dynamic modulus testing was performed with small-scale AMPT specimens collected from the CIR pavement cores.
Several findings were determined upon analysis of the test:
- The sampling method to collect field mix samples for lab compaction and testing could be a method to verify CIR mixture properties in the future.
- The dynamic modulus test results provide additional data to the industry on the performance qualities of the constructed mixture, which also align with the current industry recommendations for the mastercurves which characterize CIR materials.
This project is an excellent case study that demonstrates the outcomes that are possible when different groups are all driving to the same goal of creating longer lasting, safer roads.
Recent Comments