This past year, AMI continued to implement the 5S method within our plants to better improve safety, apply Lean principles and to support our employees at our plants. All 22 locations are trained on the 5S process by plant managers who have received their yellow belt training.
AMI completed about 19 Kaizens this past year to improve their sites using 5S. Kaizens are business activities that help improve functions and processes. The Director of Operations and Quality Control Director helps prioritize and select which locations need to perform a Kaizen.
What is the 5S Methodology?

5S is a five-step methodology that helps to create a more organized and productive workspace. The 5S’s are sort, store, shine, standardize and sustain. This methodology serves as a foundation for Lean tools and processes and was developed in Japan. It was one of the techniques that enabled Lean manufacturing.
5S Applied in Quality Analysis Lab in Iowa
Nearly every site has done a 5S-focused project, but below is one example of a recent project to organize one of our labs in Tama, Iowa. This project was unique because by reducing the footprint of existing operations, the team could convert newly open spaces into new conference rooms.
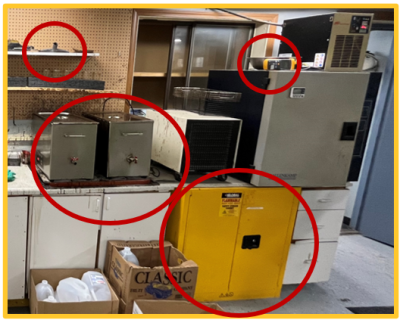
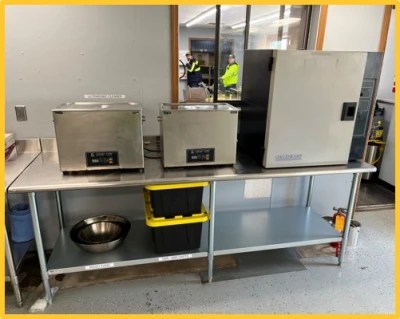
- Sort: Upon entering the lab, the team asked questions to understand what tasks are performed in the space and what items are necessary to perform those tasks. Unnecessary items were then relocated, and items including a shop vacuum attachment and bowl were moved to a more ergonomic position.
- Store: Intention is the name of the game. In addition to relocating lab equipment for less wasted operator movement, the team evaluated the space for safety storage improvements. The team also moved a cabinet out from under the oven.
- Shine: Cleaning the designated project area makes it easier to see out-of-tolerance conditions such as leaking containers and equipment in the wrong location.
- Standardize: Labeling and assigning a home for tools and equipment makes it easier to do inventory and train new employees on that process. Labels tell us what items are and what process they are for.
- Sustain: The last step is sustaining the gains developed during the project. AMI uses a standard template that shows what “good” conditions are as a reminder to the process owner and to hold others accountable for sustained organization. These templates are then posted in designated areas as a reminder.
Results
Overall, implementation of this methodology leads to improved safety, applies Lean principles and helps support our employees. In this example, the team improved safety through reducing the risk of chemical spills or burns, applied Lean principles through waste removal and supported employees by converting an old space into a designated conference room.
Recent Comments